From data silos to enterprise visualization: unlocking the full potential of your data
Fujitsu / September 4, 2024
Data has become an invaluable asset in manufacturing, driving operational efficiency, decision-making, and innovation. However, its true potential often remains untapped due to challenges like data silos and lack of visibility across the supply chain and enterprise operations. Data silos – where insights are locked away in isolated systems – hinder information flow, leading to inefficiencies and missed optimization opportunities. Without a holistic view of operations, manufacturers struggle to make informed decisions. As digital transformation becomes critical in manufacturing, overcoming these hurdles is essential.
Contents
- Understanding data silos
- Common signs and symptoms of data silos
- Enhancing data connectivity to enable end to end visibility
- From data silos to enterprise visualization
- Exploring enabling technologies with Fujitsu
- Achieving enterprise visualization in modern manufacturing
- Getting started with Fujitsu
Understanding data silos
In modern manufacturing, data silos occur when data is collected, stored, and managed by a single department or system without being shared with other parts of the organization. This isolation can happen for various reasons, including legacy systems that lack interoperability, departmental boundaries, or simply a lack of cohesive data management strategy.
Data silos impede the seamless flow of information across an organization, causing departments to miss out on the synergy of integrated data. For example, if production lacks access to real-time sales data, it can result in overproduction or stockouts. Similarly, without visibility into operational inefficiencies flagged by the quality control team, maintenance may face unnecessary downtime. Often, operational teams are unaware that their transactional data holds value for other departments.
Common signs and symptoms of data silos
Identifying data silos within an organization is the first step towards dismantling them. Here are some common signs and symptoms:
・Inconsistent data: Different departments report different figures for the same metrics due to separate data sources.
・Lack of real-time information: Teams rely on periodic reports rather than real-time data, causing critical lags in responding to market changes or operational issues.
・Redundant data entry: Employees enter the same data into multiple systems because there is no integrated platform, wasting time and increasing the risk of errors.
・Limited data access: Access to certain data is restricted to specific departments, limiting collaboration and informed decision-making.
・Inefficient reporting: Generating comprehensive reports is cumbersome and time-consuming because data must be manually consolidated from various sources, resulting in outdated or incomplete reports.
・Poor collaboration: Departments operate independently with little collaboration, leading to products or decisions that don't meet market needs.
・Fragmented decision-making: Decisions are often based on incomplete or outdated information, leading to suboptimal outcomes.
Enhancing data connectivity to enable end to end visibility
Interconnected data systems are crucial in modern manufacturing. By breaking down data silos and creating seamless information flow, manufacturers can achieve new levels of operational efficiency and innovation. Interconnected data systems ensure that information is readily accessible across all departments, enabling more informed decision-making and coordinated efforts.
For example, when a production planner integrates real-time data from sales, inventory, and supply chain systems, they can dynamically adjust the schedule to match demand. This responsiveness reduces waste and optimizes resource utilization. Similarly, maintenance teams equipped with real-time machine performance data can predict breakdowns, and order replacement parts in advance, minimizing downtime and extending equipment lifespan.
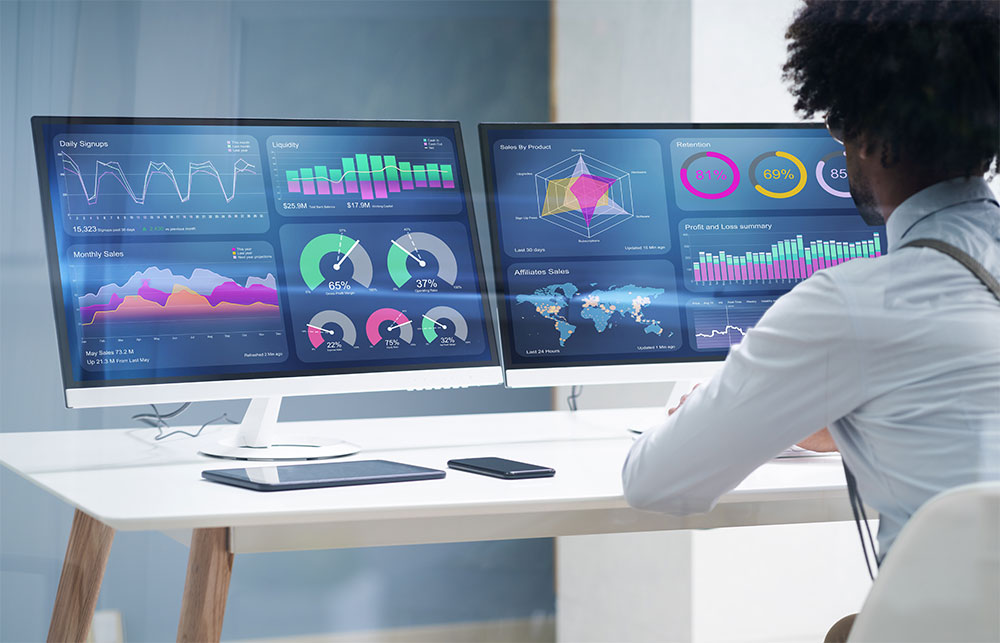
Achieving enterprise visualization involves several critical steps to ensure data is effectively collected, integrated, and accessible throughout the organization. Here are some key approaches:
1. Integrating IoT devices and sensors for real-time data collection
The Internet of Things (IoT) revolutionizes how data is collected and utilized in manufacturing. By deploying IoT devices and sensors across production lines, manufacturers can capture real-time data on various parameters such as temperature, pressure, and machine vibrations. This data provides a granular view of operations, enabling both immediate adjustments and long-term optimizations. For instance, IoT sensors can monitor machine health continuously and trigger maintenance alerts when anomalies are detected, significantly improving operational efficiency and reducing maintenance costs. Additionally, analyzing this data can detect trends in aging equipment, increasing the likelihood of acquiring hard-to-find parts before they are needed for critical repairs.
2. Implementing data integration platforms and middleware
To harness the full potential of data, it’s crucial to integrate disparate systems like Manufacturing Execution Systems (MES), Enterprise Resource Planning (ERP) systems, Procurement, Trade and other IT platforms. New techniques in data integration leverage AI and machine learning to ease the burden of bridging these “apples to oranges” systems. Next-gen integration patterns deliver on the promise of operational agility, ensuring that production schedules align with supply chain logistics and customer orders, allowing for real-time updates and adjustments, improving overall workflow and reducing lead times.
3. Establishing data standards and governance policies
With AI-powered data tools and the expansion of enterprise large language models, comprehensive data governance policies and effective data management have become more crucial than ever. Data standards ensure that information from different sources is cohesive, setting parameters to detect data anomalies before they are inadvertently incorporated into decision-making. Data governance policies define how data is managed, shared, and protected, ensuring both privacy compliance and intellectual property protection. A pragmatic application of these techniques within the manufacturing footprint includes extending standard, system-agnostic metrics definitions across all plants. Using AI tools to easily aggregate and analyze disparate data facilitates accurate benchmarking and performance comparisons.
4. Utilizing advanced analytics and visualization tools
Once data is integrated, the next step is to leverage advanced analytics and visualization tools to transform raw data into actionable insights. Implementing AI-assisted analytics software, particularly when powered by high-performance-computing, allows data science teams to process large datasets, perform complex calculations, and uncover hidden patterns. Tools like Palantir, Hadoop, Spark, and machine learning algorithms are invaluable in this process. Other teams that commonly work with data can use visualization platforms such as Tableau, Power BI, or custom-built dashboards to create interactive and dynamic visual representations of the data. AI can enhance these platforms by improving design and support tools for casual users, thus removing the "report builder barrier" and making data accessible for daily decision-making.
5. Ensuring data accessibility across the organization
For enterprise visualization to be effective, data must be accessible to all relevant stakeholders within the organization. While user-friendly tools are important, promoting a culture of data democratization is even more crucial. This means making data available to employees at all levels and connecting data-driven insights to delivering business value. It involves making data stewardship and compliance "everyone’s job" and ensuring that employees have the necessary training to interpret and utilize the data effectively. Additionally, every organization needs a qualified team in place to develop policies and implement robust access controls and security measures to protect sensitive data while ensuring that authorized users can access the information they need.
From data silos to enterprise visualization
These advances also impact how data is represented. Enterprise visualization involves transforming complex and fragmented data into cohesive, interactive visual representations that provide a comprehensive view of an organization's operations. Visualization is how data tells its story. Unlike traditional data reporting, which often presents static and siloed snapshots, enterprise visualization integrates data from multiple sources and presents it in dynamic, easy-to-understand formats such as dashboards, charts, and real-time data feeds. A well-designed visualization can equalize understanding of the data set across functions, improving collaboration and accelerating decision-making.
Benefits of enterprise visualization
・Holistic view of operations: Enterprise visualization offers a unified view of data from different departments and systems, enabling stakeholders to see the big picture and understand how various components of the business interact.
・Improved decision-making: By providing cohesive collaboration tools, real-time insights and highlighting trends and patterns, enterprise visualization aids in making informed, data-driven decisions quickly.
・Increased transparency and accountability: With accessible and clear visual data, organizations can create greater transparency and accountability at all levels. Employees can understand their impact on the overall operations, and leadership can monitor performance against strategic goals.
・Enhanced communication and collaboration: Visual data is easier to share and discuss across teams, promoting better communication and collaboration within the organization.
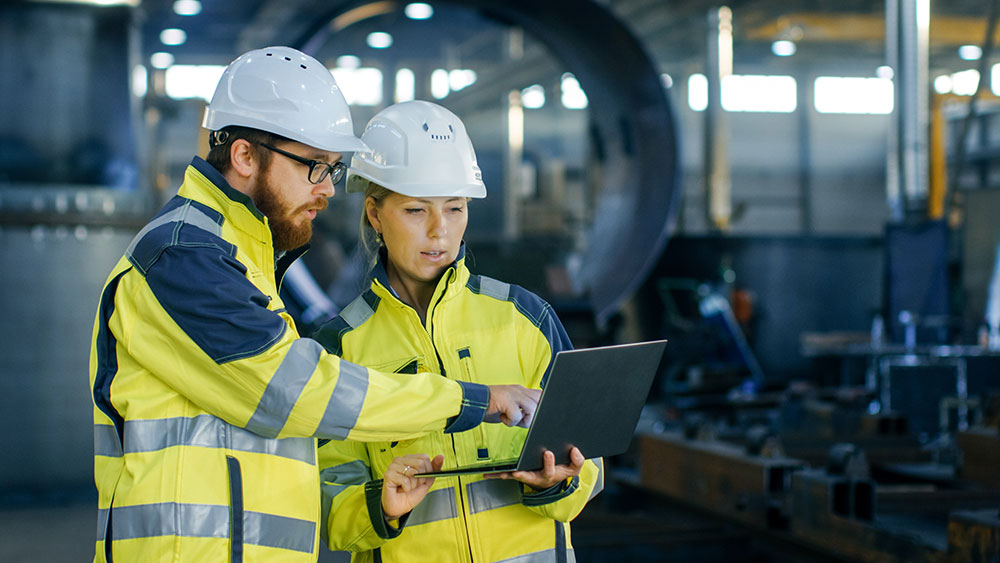
Exploring enabling technologies with Fujitsu
As a manufacturer ourselves, Fujitsu has long sought better tools for understanding and optimizing operations. With this heritage, Fujitsu is at the forefront of integrating advanced technologies to enhance enterprise visualization capabilities. By leveraging a suite of digital tools and platforms, including our own unique technologies, we help organizations break down data silos, achieve real-time insights, and drive operational efficiency. Our holistic approach ensures that manufacturers can harness the power of technologies like AI, high-performance-computing, digital twins, big data analytics, and blockchain to create a cohesive and dynamic data environment.
1. Digital twins
Digital twins are a terrific example of how these technologies can be used together to improve operations. A digital twin is a virtual replica of physical assets, processes, or systems that allow a manufacturer to simulate, analyze, and optimize their operations in a digital environment. By creating a digital twin, manufacturers can mirror the real-world behavior of their people, equipment and processes, providing a detailed and dynamic representation that can be used for informed decision-making and action planning.
・Predictive maintenance: Digital twins enable continuous monitoring of equipment health, allowing for the prediction and prevention of potential failures before they occur. This proactive approach minimizes downtime and extends the lifespan of machinery.
・Process optimization: By simulating different scenarios, digital twins help identify the most efficient and cost-effective ways to optimize production processes. Manufacturers can test changes in a virtual environment before implementing them in the real world, reducing the risk of disruptions.
・Scenario testing: Digital twins allow manufacturers to run various "what-if" scenarios to assess the impact of different variables on their operations. This capability is invaluable for strategic planning and decision-making.
2. Big data analytics
Big data analytics is also important for manufacturing. These techniques involve processing and analyzing large volumes of data to uncover patterns, trends, and insights that can drive informed decision-making. In the manufacturing context, big data analytics is crucial for understanding and optimizing every aspect of production.
・Real-time monitoring and analysis: Big data analytics tools enable real-time monitoring of production data, allowing manufacturers to identify inefficiencies and optimize processes on an ongoing basis. This continuous feedback loop helps maintain optimal performance.
・Data science: Technologies like Palantir, Hadoop, Spark, and machine learning algorithms are essential for processing vast amounts of data quickly and efficiently. These tools help in uncovering hidden patterns and generating actionable insights, which in turn allow for improved decision-making through data-driven insights and an enhanced ability to anticipate and respond to market changes.
3. Blockchain
Blockchain is a frequently misunderstood but vital tool in the Industry 4.0 toolbox. This technology provides a decentralized and immutable ledger of transactions and data entries. In a multi-tiered, complex supply landscape, blockchain ensures that data cannot be altered or tampered with and ensures that data is accessible when and where it is needed. Given the compliance and traceability needs of manufacturers, it is impossible to overstate the value immutable data can bring to an organization, making it highly reliable for maintaining data integrity and transparency.
・Supply chain traceability: Blockchain can track the movement of goods throughout the supply chain, providing a transparent and verifiable record of each transaction. This traceability is crucial for ensuring product authenticity and quality.
・Quality control: By recording quality control data on a blockchain, manufacturers can ensure that the information is accurate and tamper-proof. This helps in maintaining high standards and building trust with customers.
・Compliance: Blockchain can simplify compliance with regulatory requirements by providing an auditable trail of data entries and transactions, ensuring that manufacturers meet all necessary standards.
Achieving enterprise visualization in modern manufacturing
Breaking down data silos and achieving enterprise visualization is a strategic imperative for modern manufacturing. As we’ve explored, data silos hinder operational efficiency and decision-making, while enterprise visualization empowers organizations with a holistic, real-time view of their operations.
Now is the time for manufacturers to consider how enhanced data connectivity can benefit their operations. By integrating technologies such as digital twins, big data analytics, and blockchain, organizations can transform isolated data into actionable insights, driving significant improvements across their operations. Fujitsu supports organizations at all levels of digital maturity in this transformation, offering expertise and solutions to help manufacturers achieve enterprise visualization and remain competitive in their market.
Getting started with Fujitsu
Is your organization ready to embrace the enabling technologies that can drive progress and unlock new opportunities for growth and efficiency? Speak to Fujitsu’s Sustainable Manufacturing experts. Together we can evaluate your current data management practices, identify existing silos, and take proactive steps towards building an interconnected and transparent data ecosystem.
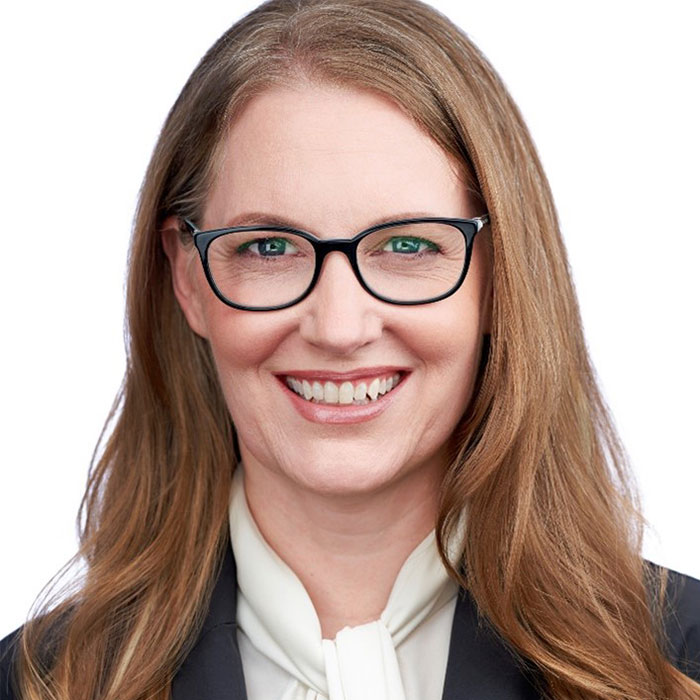
Editor's Picks
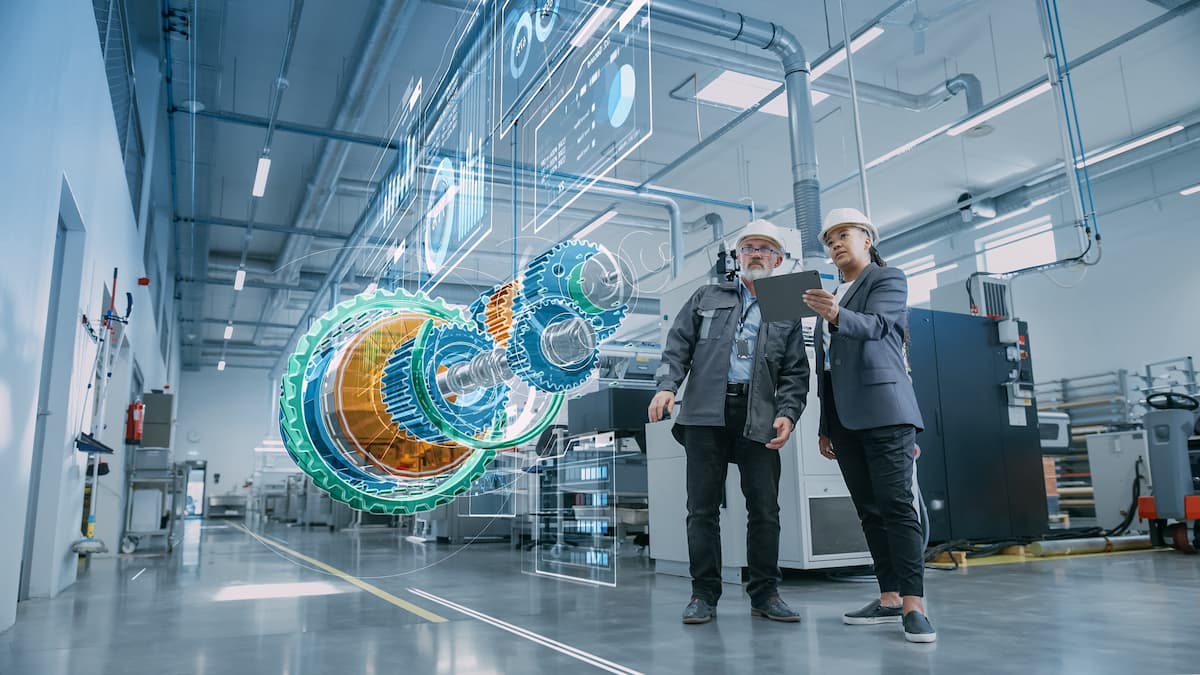
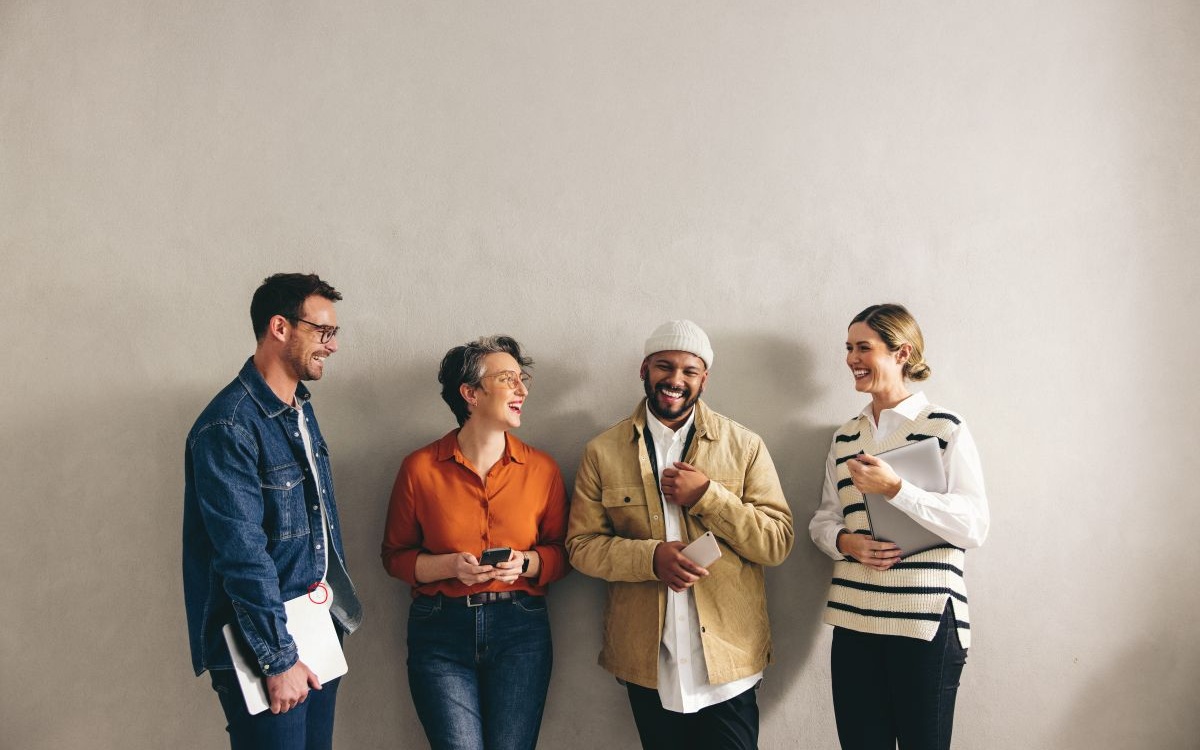
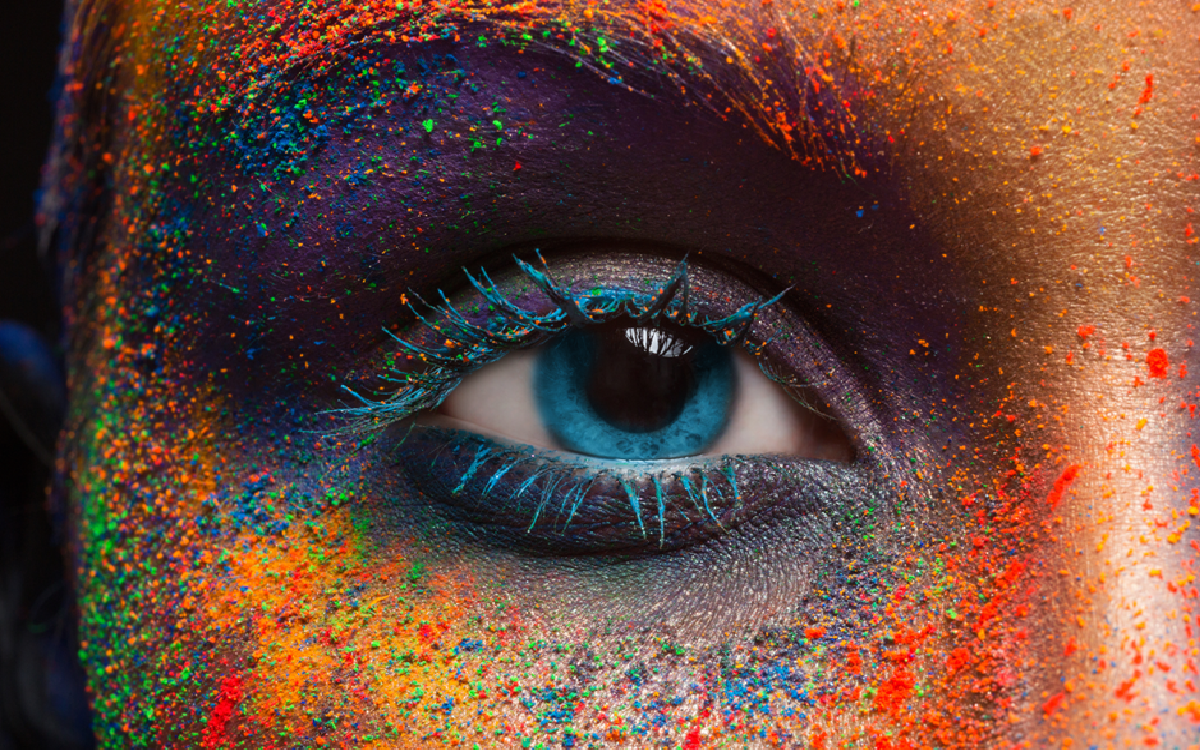