Enter the Smart Factory: Future-proofing manufacturing with sustainable digital transformation
Fujitsu / November 16, 2023
In today’s manufacturing landscape, there's a perceived tension between growth and sustainability. Manufacturers grapple with the desire to expand, yet remain committed to conservation and efficiency. Central to both desired outcomes lies digital transformation. Far from being just about the latest technologies, digital transformation blends sustainable practices with advanced digitization. This synergy not only boosts growth but also refines processes, enhancing efficiency across operations.
Today's manufacturers prioritize more than just tangible outputs. They're also aligning with an ethical blueprint, valuing every resource – be it human or material. By adopting a sustainable approach, manufacturers aren't focusing solely on immediate gains. They're creating a future that champions responsible, sustainable business growth in sync with their community.
The evolution of the smart factory
Paths to digital manufacturing
The manufacturing world today is, in many ways, a tale of two cities. Each with its unique priorities, challenges, and aspirations. On one side, we have the new-age pioneers: the smart factories. Establishments conceived in the digital age, built with a foundation that inherently integrates the principles of digitization. Then, contrasting this modern landscape, we have the legacy factories that have stood the test of time, but now find themselves at a pivotal juncture.
Smart factories: The digital natives
Smart factories are the embodiments of the digital era in manufacturing, often referred to as having a 'digital DNA.' From their inception, they have been integrated with cutting-edge technologies, ensuring seamless connectivity, real-time data analysis, and agile operations. Reshoring initiatives have also seen many businesses preferring to build these smart factories closer to their primary markets. This adds another layer of efficiency in response time and reduces transportation impacts.
The greenfield approach to these factories offers immense flexibility. With no pre-existing structures or systems to modify, they can be optimized for current requirements, be it advanced 5G/6G network integration or the latest in machine execution systems (MES). But it's not just about technology. These factories often attract a younger, tech-savvy workforce that aligns well with their digital ethos, creating an ecosystem where innovation thrives.
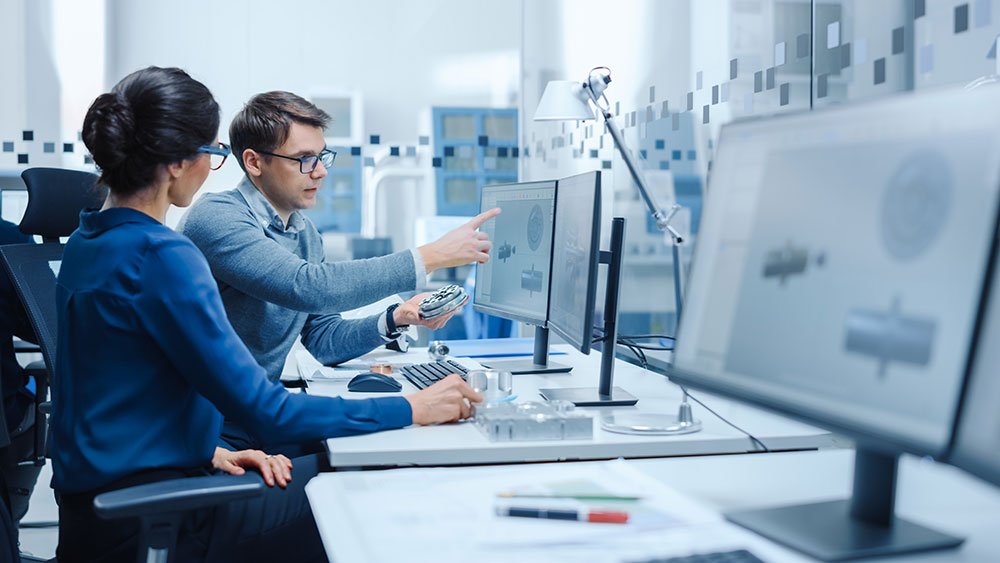
People Enablement for Digital Factory Transformation
Legacy factories: The digital migrants
Legacy factories are the established manufacturing facilities that have witnessed the ebb and flow of the manufacturing sector over the decades, with foundations deeply rooted in traditional manufacturing processes. While they bring a wealth of experience and established operational methodologies, the journey towards digitization can be a steep climb.
Modernizing these factories isn’t just a matter of introducing new technologies. It's about transforming an entire ecosystem – from outdated equipment that might not easily interface with new digital tools to an often ageing workforce that might require reskilling. The challenges also extend to capital expenditures, where substantial investments might be needed to bring about real change. Attracting a younger workforce, vital for infusing new energy and ideas, might also be challenging, given the sometimes-perceived dated environment.
Key drivers for digital transformation in legacy factories
For legacy factories, anchored in decades of tradition, the need for agility, efficiency, and a forward-looking strategy is crucial. Digital transformation represents not just the introduction of modern tools but a fundamental shift in operation, competition, and sustainability.
Efficiency is paramount. With global competition intensifying, these factories must harness digital tools to enhance productivity, reduce downtime, and streamline processes. Legacy machinery, while robust, often lags in integration capabilities. Digital initiatives bridge this, allowing old and new systems to cohesively optimize operations.
Data-driven decision-making capabilities are key to the future. With many legacy factories operating in silos, vital data remains scattered. Digital integration offers a cohesive, secure data view, ensuring responsive production strategies. While initial digital investments may seem steep, the long-term cost savings and return on investment, from predictive maintenance to optimized supply chains, are profound.
The making of the modern smart factory
The connectivity revolution: the power of 5G/6G
Connectivity is the crucial force driving modern manufacturing operations. The modern era demands real-time collaboration, instant data access, and unified communication. 5G and its imminent successor, 6G, are more than just speed upgrades – they're reshaping manufacturing's horizons.
5G/6G networks, known for their ultra-reliable low-latency communication (URLLC), ensure faster and dependable data transmission. This translates to real-time feedback, immediate process changes, and seamless complex operations with minimal delays. Amplified device connectivity via these networks realizes the potential of the Internet of Things (IoT) in manufacturing. Factories now witness unprecedented device interconnectivity, integrating every sensor, machine, and system in a cohesive operational structure.
No longer do the realms of Information Technology (IT) and Operational Technology (OT) operate in silos. Enhanced connectivity bridges these spheres, creating a streamlined data flow from shop floors to executive suites, enabling nimble decision-making. A standout offering of 5G/6G is the capability for private networks, tailor-made for factories, prioritizing optimal performance and robust security amid growing cyber threats.
While 5G revolutionizes industries, 6G promises even more, including refined AI integration and potential holographic communication. By harnessing these networks, factories don't just enhance today's functions but ready themselves for the digital future, whether it's overseeing remote operations, collaborating globally, or synchronizing with worldwide partners. Central to the concept of smart factories is this connectivity, with 5G/6G at the helm, facilitating factories that can adapt, predict, and continually optimize.
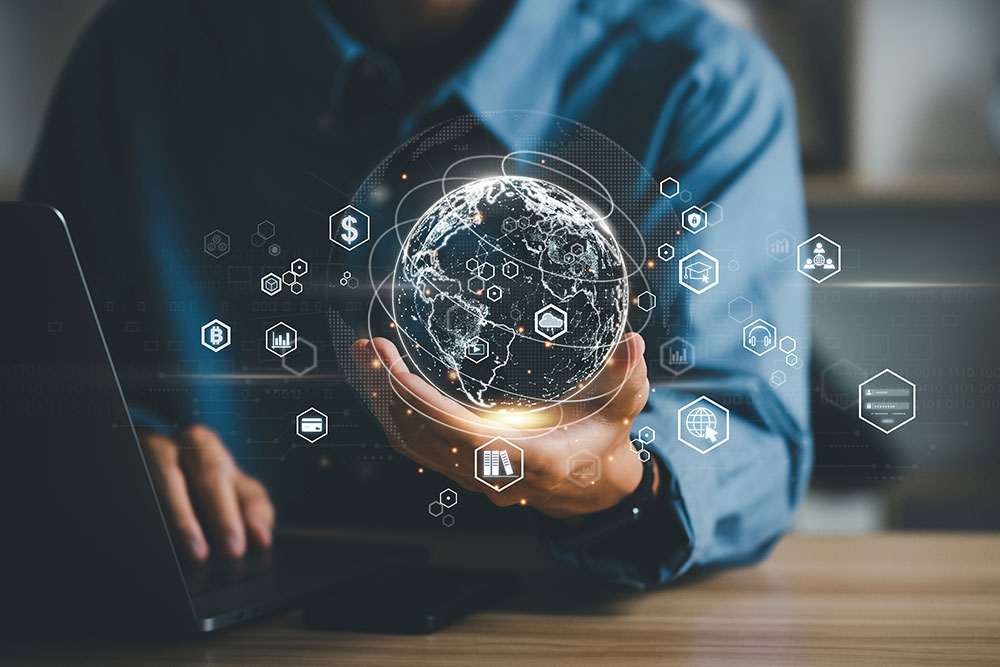
Predict, adapt and optimize Factory Operations with 5G/6G
Empowering the workforce with data and digitization
Modern manufacturing is as much about people as it is about technology. Workers, as the backbone of the industry, are transitioning from task executors to informed decision-makers, fueled by data and digitization.
Today, decisions aren't based merely on historical data or intuition. Real-time data feeds empower factory-floor workers to assess metrics, monitor equipment, and preempt disruptions. This access to data ensures rapid responses, reducing downtime and maintaining product quality. MES and Software as a Service (SaaS) platforms seamlessly integrate the physical with the digital, offering an interface for workers to engage with machinery, process data, and introduce improvements.
The Industrial Internet of Things (IIoT) and mobile devices have universalized data access, ensuring the workforce is informed, regardless of location. Coupled with the right digital tools, this access amplifies job satisfaction, boosting morale and aiding talent retention. Recognizing the skill shift digitization demands, leading manufacturers prioritize reskilling, preparing their workforce for both technical nuances and adaptive problem-solving in a digital setting.
To remain aligned with the pace of digitization, it's imperative to cultivate a culture of ongoing learning. Regular training and online resources ensure the workforce stays updated. Importantly, digitization dismantles traditional hierarchical barriers, offering everyone from technicians to managers a holistic view of operations. This inclusive visibility encourages collective problem-solving and innovation.
Bridging supply chain with the factory floor
In digital ecosystems, the once distinct realms of supply chains and factory floors have blended into a coordinated production organism. The power of digitization has provided unparalleled transparency throughout the manufacturing process, from raw material sourcing to finished product shipment. This visibility translates to informed, proactive decision-making, replacing outdated reactive approaches.
A testament to this integration is the union of MES and Enterprise Resource Planning (ERP) platforms. While MES provides insight into the nuances of production, ERP offers a panoramic view of operations from procurement to sales. This confluence ensures a fluid information exchange, amplifying both operational efficiency and profitability.
The resulting benefits are manifold: just-in-time delivery protocols, made possible by bringing together real-time production data with supply chain metrics, curtail inventory overheads. Manufacturers, equipped with an integrated digital platform, can now navigate market volatilities, reducing lead times and upholding client expectations. Moreover, as both supply chain professionals and production teams tap into identical real-time datasets, collaborative problem-solving emerges as the standard. This shared data access ensures meticulous product traceability, vital for regulatory compliance and building consumer trust.
Further, the unified digital framework facilitates predictive analytics, enabling manufacturers to anticipate equipment issues, minimize unexpected downtimes, and optimize resource deployment.
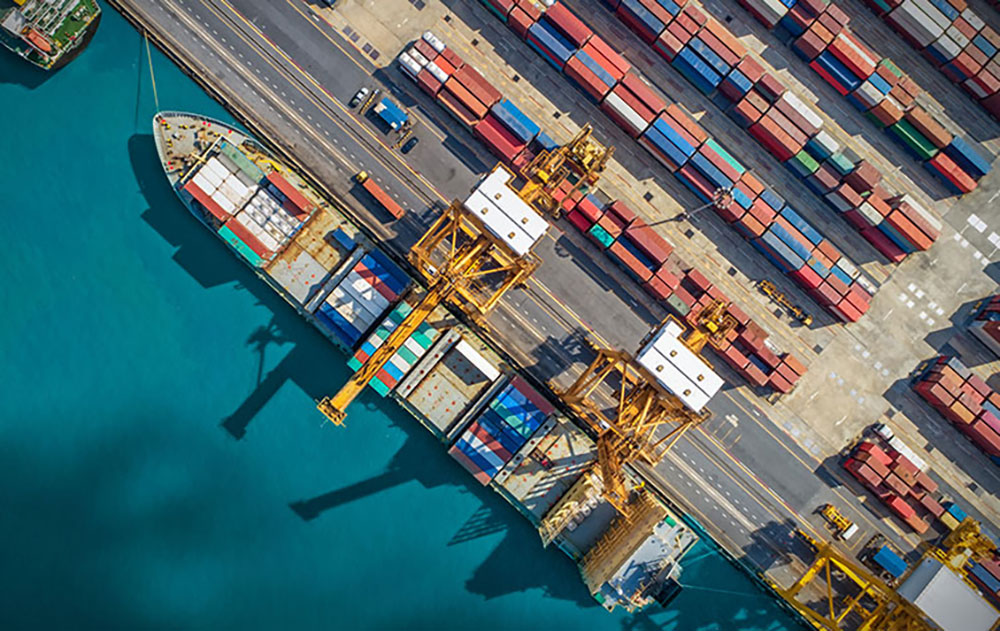
Digital Supply Chain Optimization
Automating and reskilling: addressing labor shortages and enhancing safety
Automation and human skills are increasingly intersecting in today’s manufacturing, presenting both challenges and opportunities. While automation enables efficiency and precision, the human touch offers adaptability and critical insight. The crux lies in leveraging both to address labor shortages and enhance workplace safety.
Automation, through tools like cobots and Automated Guided Vehicles (AGVs), help manage repetitive tasks and fill labor gaps, complementing human roles. Simultaneously, its ability to function in hazardous settings minimizes human risk and prioritizes workforce safety. However, as automation grows, the nature of human roles transforms. Instead of replacing humans, automation necessitates their evolution into more nuanced, value-added tasks. This shift underscores the criticality of reskilling, enabling workers to navigate new roles, from overseeing automated systems to maintaining advanced machinery.
But reskilling isn't solely a reactive measure; it's a proactive step towards the future. Manufacturers committed to regular training ensure their workforce remains agile, ready to harness emerging technologies and contribute to a dynamic production environment. Contrary to fears, automation, when approached strategically, can bolster job security. Reskilled employees, equipped with unique competencies, find purpose in roles beyond machine capabilities. Moreover, commitment to employee growth fosters loyalty, as retention hinges on carving viable career paths for workers.
AI and quantum-inspired computing: analyzing the deluge of factory data
The exponential data influx in today’s factories demands swift analysis and actionable insights to drive operational excellence. While traditional computing offers some solutions, it often falters against the magnitude and intricacy of factory data. Here, Artificial Intelligence (AI) and quantum-inspired computing are elevating data analysis capabilities.
AI, with its pattern recognition abilities and predictive analytics, is transforming factories. By forecasting machinery failures, streamlining production, and enhancing quality control, AI converts raw data into real-time, actionable strategies, improving efficiency and product standards.
Quantum-inspired computing, though in its nascent stages, already showcases its potential through solutions that imitate quantum computers' parallel processing on conventional hardware. This translates to heightened computational speeds, especially crucial for the intricate challenges of manufacturing.
Fujitsu, as an innovator in this domain, offers a computational architecture known as the Digital Annealer, which utilizes quantum principles to solve complex optimization issues without needing quantum environments. This tool provides insights ranging from refining factory logistics to amplifying supply chain proficiency. The Fujitsu Kozuchi platform is an example of AI's transformative role in manufacturing, integrating with factory systems and deploying advanced AI algorithms for enhanced operational insights.
However, AI and quantum-inspired computing's influence transcends mere data analysis. They pave the way for an agile, responsive, and intelligent production arena. With applications as diverse as optimizing production layouts or real-time inventory oversight, tools like Digital Annealer and Kozuchi highlight the transformative potential of contemporary computational solutions.
Increasing the odds of smart factory success
Taking a deliberate path to digital transformation
Given the pace of change, manufacturers might feel pressed to adopt every innovation. Yet, the essence of effective digital transformation isn't mere adoption but a well-considered approach, tailored to business challenges and objectives. Rather than starting with technology, successful digital transformation zeroes in on existing business challenges. Recognizing inefficiencies, labor gaps, or market demands ensures that digital strategies are precisely targeted and outcome oriented.
It's vital not to get swept up in hype cycles. Instead, manufacturers should appraise each technological solution against their goals, pinpointing those that dovetail with the company's broader vision. This evaluation process means forgoing fleeting trends in favor of impactful, measurable benefits.
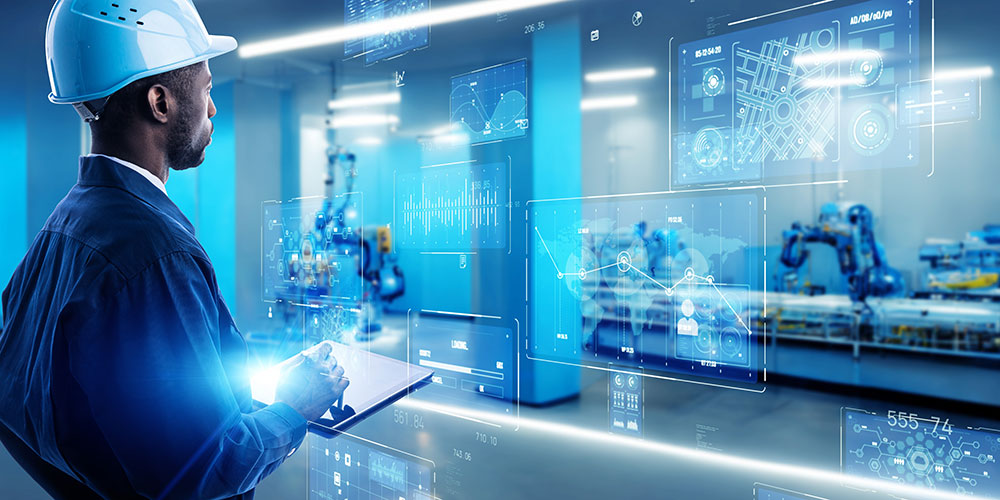
The path to Digital Transformation
Embracing the digital shift
Manufacturing is at a crossroads, driven by dynamics both intrinsic and extrinsic to the sector. Navigating this landscape depends on embracing digital transformation. This transformation transcends technology adoption; it's a profound reimagining of mindset and operations. The goal isn't merely operational efficiency but sustainable, holistic growth that integrates the workforce, environment, and innovation.
This convergence of established manufacturing principles and a digital native ethos paves the way for production that's both efficient and ethical. Fujitsu, having experienced the challenges of transformation first-hand through our own factory network, goes beyond providing digital tools. Our vision is to reshape the realm of possibilities for our customers by offering everything necessary for robust, future-focused decision making. As the industry evolves, we believe that success depends on taking a deliberate path towards an ethical, and efficient manufacturing future.
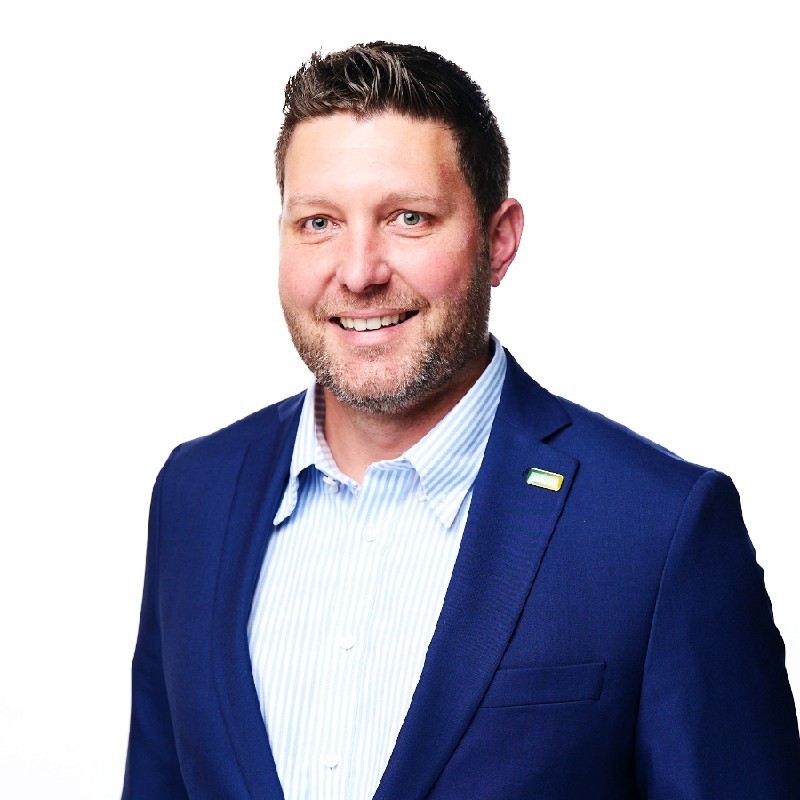
Johan’s overall focus has been on the digital enablement and automation of key manufacturing capabilities and ability to drive compelling value to Fujitsu clients.
Editor's Picks
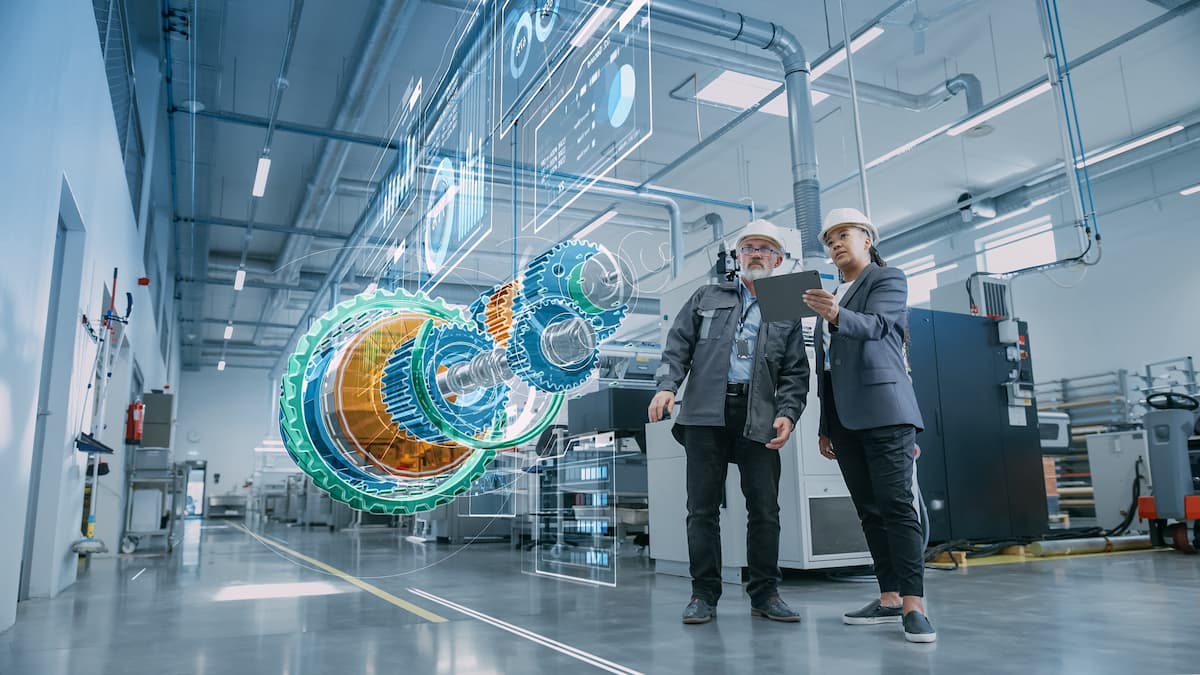
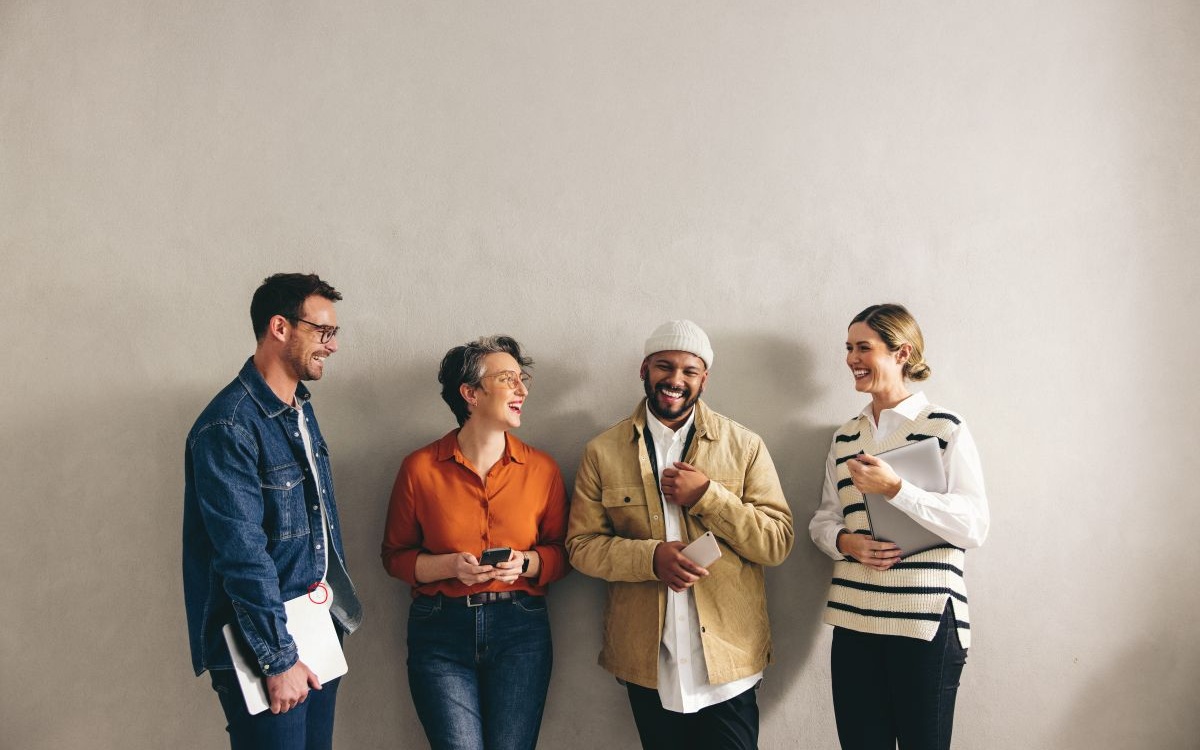
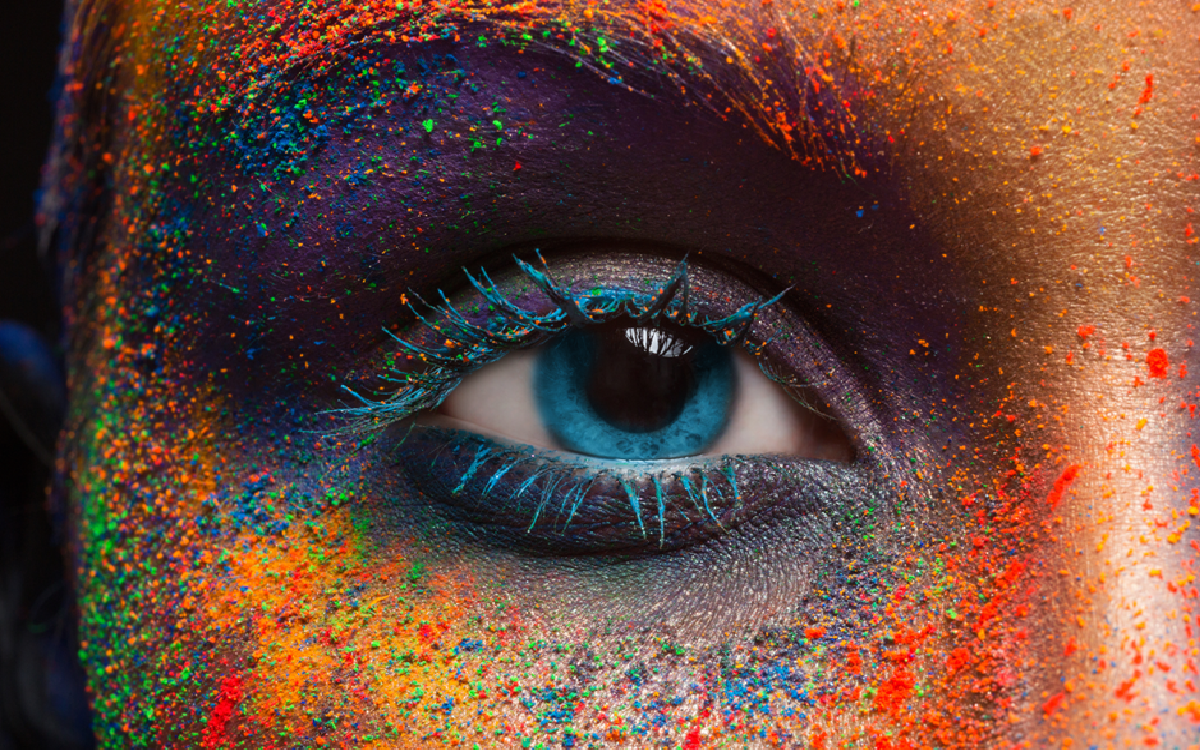