How innovation enables environmental responsibility and improves workforce wellbeing in manufacturing
Fujitsu / December 14, 2023
The most important resource in any organization is its human capital. Combined, this resource provides the collective knowledge, attributes, skillsets, and overall experience, which determine the overall health of a business. Manufacturing is no different.
In fact, the manufacturing industry needs to do more to meet the wants and needs of a workforce. At the present time, manufacturers need to either adapt or fall behind, not just in terms of their production equipment, but in respect to developing a more connected workforce.
The next generation of manufacturers are now entering the workplace, and they have different priorities. They want to work with the latest digital solutions, embracing change rather than being wary of it. All while working for an organization that prioritizes sustainability. This change is also currently taking place amidst ongoing labor issues and workforce shortages, as well as the changing expectations of the modern manufacturing worker.
This highlights an opportunity for manufacturers. Investing in digital tools will not only help them work smarter and improve productivity, but do so in a more efficient, engaging manner. Manufacturers who successfully unify their people, processes and machines can enhance not only their bottom line and workplace morale but also achieve these improvements while simultaneously pursuing sustainability goals.
Connecting your people
To operate at an optimal level, manufacturers require a workforce with the ability to adapt rapidly to changing circumstances and take on new tasks or responsibilities. Often those that require different, often varied skillsets. Instead, the traditional workforce is ageing and new recruits with the right skills are in short supply and high demand. Many companies are also relying on overseas or short-term workers to fill gaps which only adds an extra threat of instability.
Amidst these challenges, manufacturing companies can look for transformative digital solutions that not only help address the issue, but support broader initiatives centered around sustainability.
Alleviating staff turnover
Manufacturing sees a great deal of staff turnover. This is generally due to the perception of a workplace environment which is not considered attractive relative to other jobs. It has historically been seen as a physically demanding career option – a viewpoint which has carried on into the digital, “Industry 4.0” era.
However, when companies start integrating digital solutions into their overall factory operations a new story emerges. Digitalization creates a safer, less physically demanding factory floor. And with this change, manufacturing can be framed through the lens of a desirable career rather than a short-term job.
Yet the association of automation and digitalization with manufacturing has typically been viewed as a net negative by the public. These advancements are perceived as a destroyer of jobs, communities, and a threat to the working population. Manufacturers must counter this narrative by focusing on people-centric transformation. They can look to automation that specifically targets the repetitive, dangerous, and mundane tasks that would potentially put people at risk.
Digitalization also creates the opportunity for career growth, offering traditionally skilled manual workers the opportunity to move into digitally skilled operator roles, thereby increasing job security, satisfaction, and appeal. This safeguards employee well-being while meeting production demands, offering a balanced approach to modern manufacturing challenges.
Technology as an enabler
In a highly competitive global marketplace, early adoption of innovative solutions will be critical to achieving the objectives of a manufacturer’s broader industrial strategy. But without the right workforce, manufacturers will miss their chance to stand out in the marketplace. Technologies — whether existing or emerging — are of zero value if they do not enable people with the right skills to make the right decisions.
Manufacturing organizations need to be ready to facilitate this change. Workers are now using more advanced technology in their daily lives each year and they expect to see the same level of technical capability in their jobs. The right technology is within reach. Incorporating mobile and IoT devices – such as tablets or other intuitive technologies – on the factory floor helps connect workers to machines. This type of ‘digital transformation’ improves worker engagement and gathers the data necessary for real-time decision making. Following which, more efficient operations are a natural outcome of these types of informed insights.
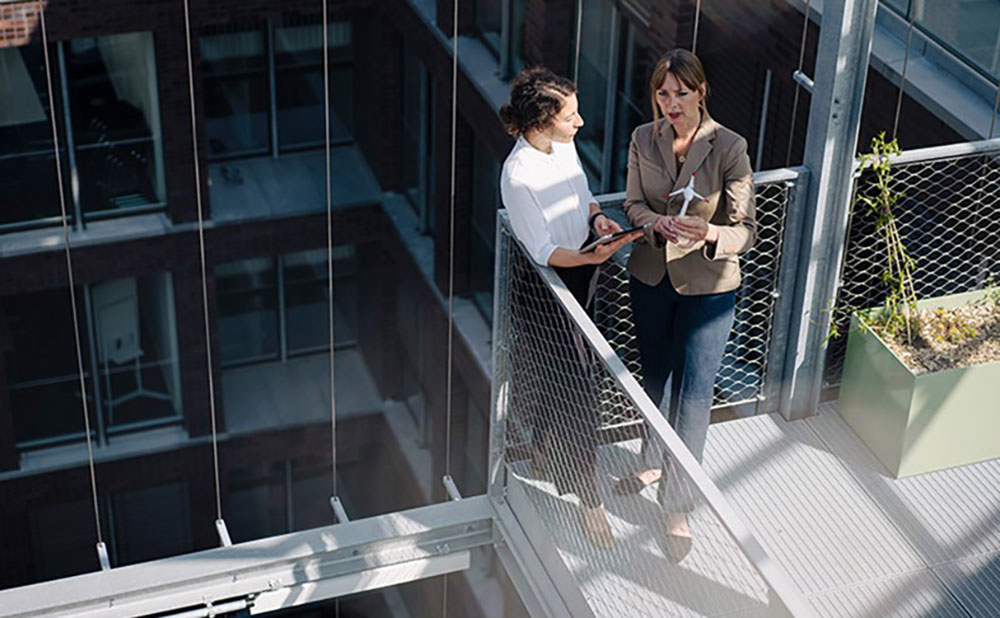
Innovation in Action: Digital tools empower workers, fostering collaboration and creative problem-solving in modern manufacturing.
In turn, this approach creates collaborative opportunities for workers, both those on the factory floor as well as those operating in different geographic locations. They are able to share knowledge and communicate easily. This matters because some of the best, most impactful ideas often come directly from the talent on the factory floor. Manufacturers should therefore be looking to use automation and digital technologies to free up their workforce, allowing employees to then devise more creative solutions to current industry challenges.
Sharing knowledge
When facing the threat of high staff turnover, digitalization is a reliable and proven strategy for continued gains in efficiency and productivity. With an aging and shrinking workforce, manufacturers face a growing skills-vacuum that hinders productivity and imposes additional costs to an organization. Digital solutions - AR and VR being prime examples - promote upskilling and enhanced learning processes among manufacturing workers. Training is then made more engaging and effective for new personnel.
By developing a digital platform for knowledge-sharing that can constantly be updated as new solutions emerge, workers can quickly upskill and increase the value they offer, supporting both the company and their career goals. When powered by low-latency and ultra-reliable connectivity solutions, these platforms also overcome the constraints of geographical locations as experts in other facilities can share knowledge directly without the need for travel.
Connecting with your wider community
Despite increased levels of automation, the ecosystem that surrounds a manufacturing facility is just as important as what takes place inside one. Effective manufacturing operations require good supplier relationships and the application of local skills and capabilities. Simply put, manufacturing creates strong communities.
Historically, a manufacturing facility was the cornerstone of a community. A factory was an employer of generations of local workers; they would invest in local sports teams and other community endeavors, and often their financial success would impact the quality of life in the surrounding area. Uprooting or closing a manufacturing plant would therefore not just affect the economic vibrancy of a community, but its cultural make-up as well.
Cultural shifts and workforce engagement
When towns and cities see their cultural identity centered around manufacturing, digital transformation takes on a tone of civic responsibility. Community members and workers want to see their local industry become more technologically driven, and, crucially, more sustainable. People want to work for companies that align with their values and, with increasing frequency, that includes reducing environmental impact and supporting sustainability initiatives.
Manufacturers are facing pressures from regulatory bodies pushing for progress on environmental performance, but so too are the communities they are looking to establish relationships alongside. Everyone has a stake in this game. Tools such as a corporate sustainability plan that is rooted in achieving positive local impact can improve pride-in-work and general employee morale, positively impacting overall productivity. Since these steps often mean solving for regulatory requirements, manufacturers achieve a double win. Here, digitalization is the path to achieving both objectives.
Conclusion – An entire ecosystem in operation
Human capital is much more than just numbers on a spreadsheet. Each member of a workforce makes a unique contribution to an organization’s success. Sustainable success is therefore people centric.
Considered in isolation, what’s good for productive output may in fact have negative effects on other important areas such as the workforce and the surrounding community. It’s by understanding the full ecosystem, and how its parts interconnect, that digitalization can be applied to support better manufacturing outcomes.
Fujitsu's comprehensive solutions put the worker at the center, and therefore not only lead to positive business outcomes but alleviate pressing industry concerns relating to talent shortages, people enablement, and carbon footprint reduction.
By offering advanced digital solutions and strategies, Fujitsu supports manufacturers to not only optimize operations, but also help them showcase a commitment to sustainability, to their workforce, and to a future which prioritizes both.
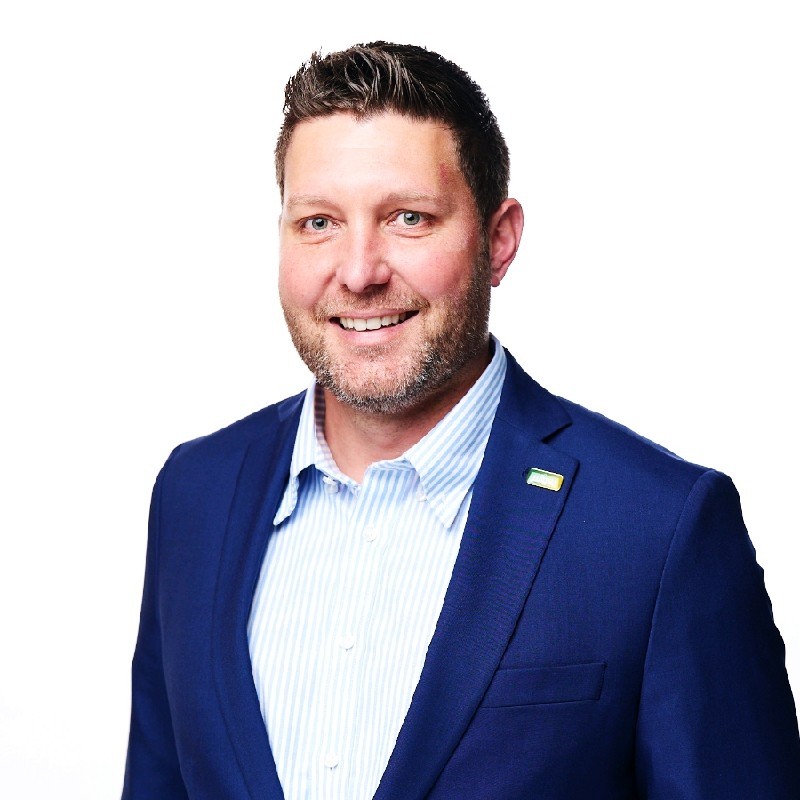
Johan’s overall focus has been on the digital enablement and automation of key manufacturing capabilities and ability to drive compelling value to Fujitsu clients.
Editor's Picks
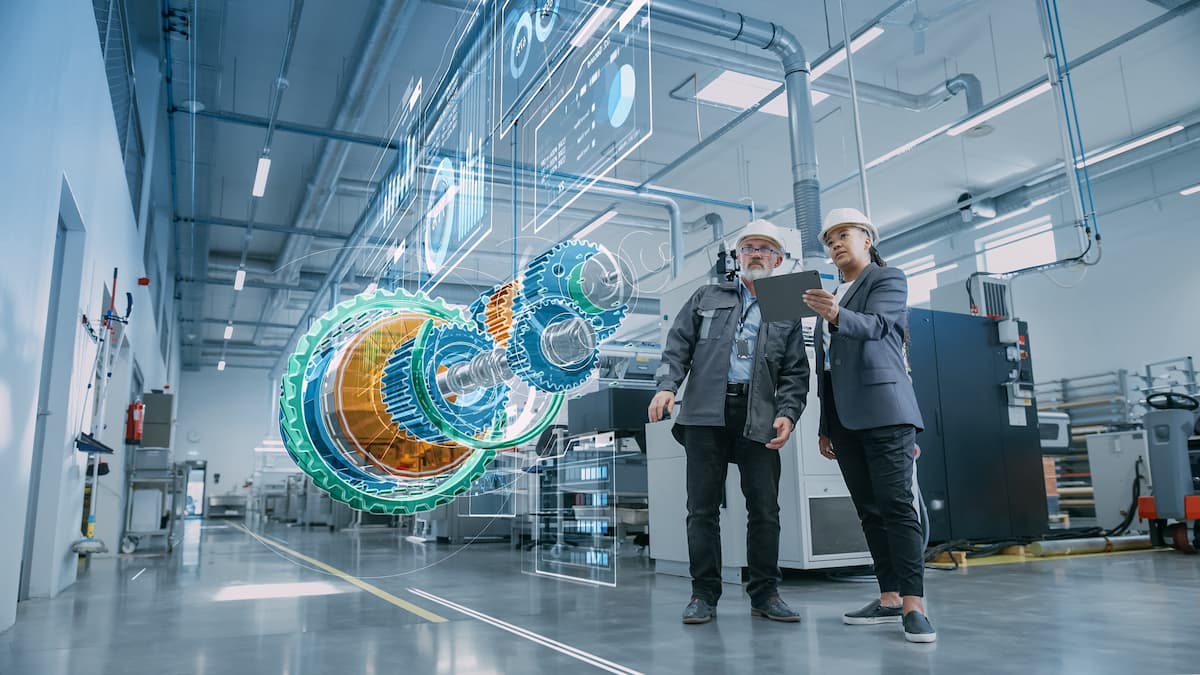
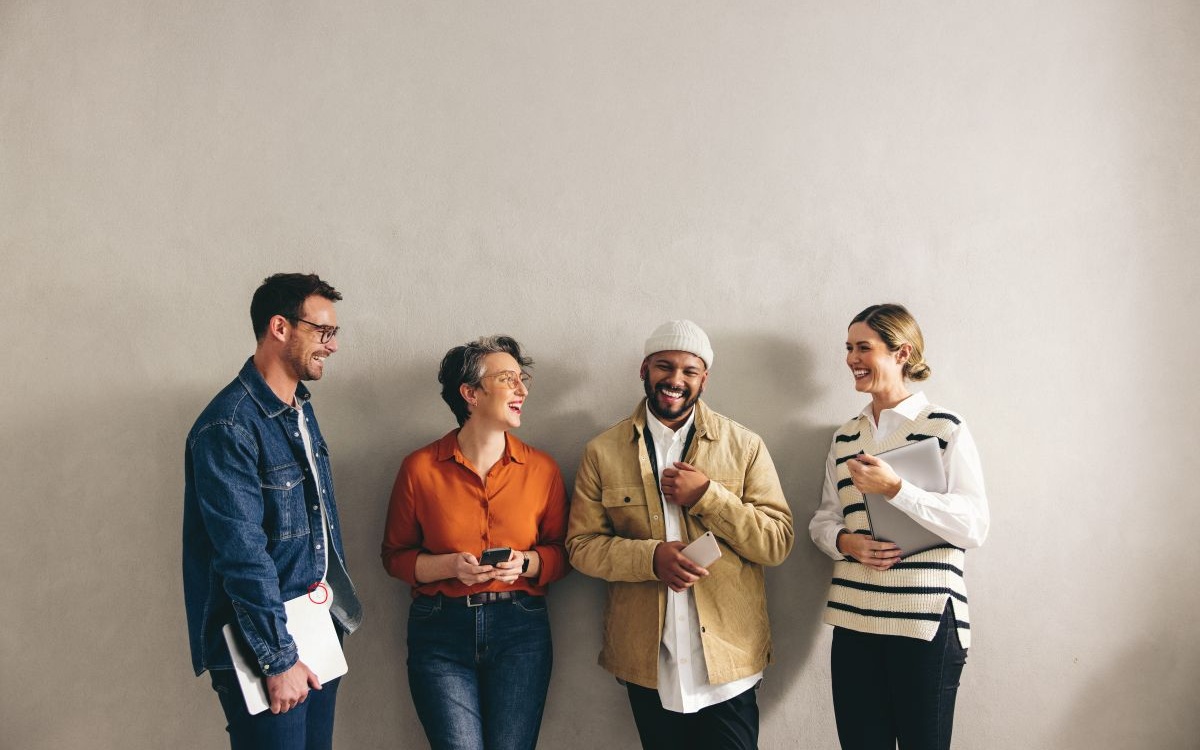
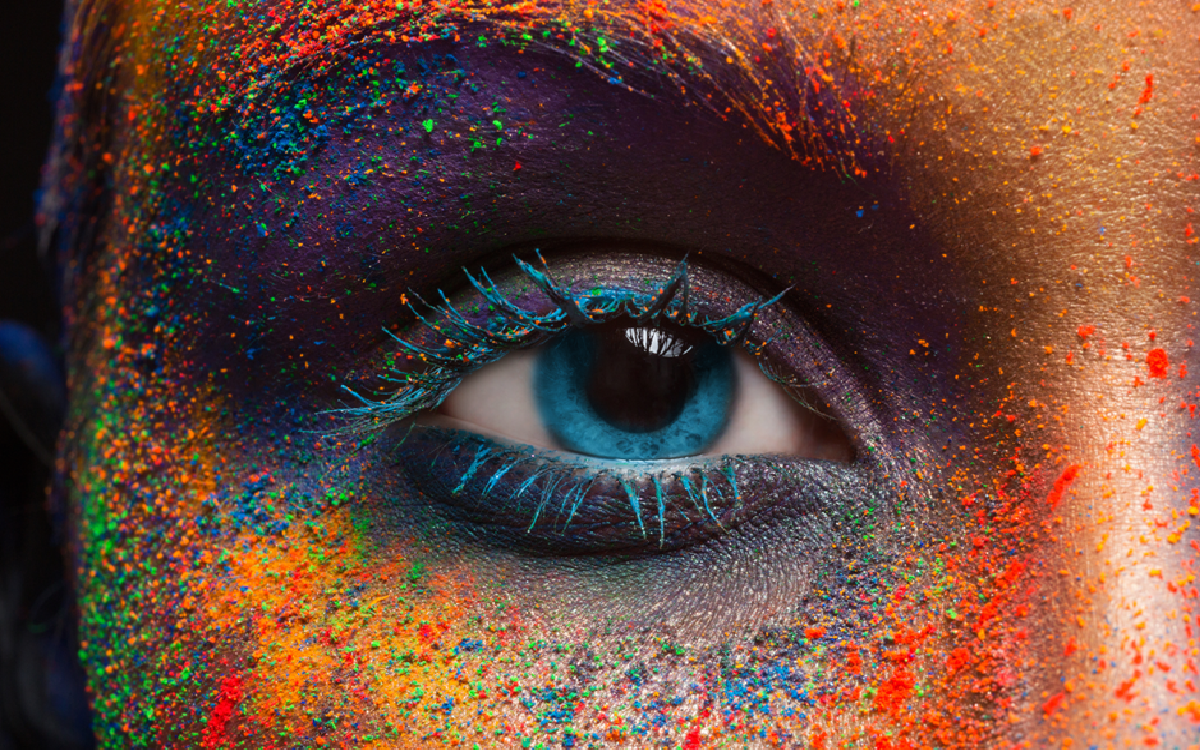