The pursuit of efficient manufacturing: How data visibility supports waste reduction
Fujitsu / November 29, 2023
Today’s manufacturing decision-makers find themselves in a difficult position. There is a constant expectation on one side for repeated expansion and growth, which is seemingly opposed to the growing demands for more sustainable operations.
Manufacturing is particularly vulnerable to this precarious balance. As a whole, traditional manufacturing has been a major contributor to global carbon emissions and waste products. However, regulations aimed at promoting sustainability are set to change these conventional ways of operating.
Modernization is therefore needed. But manufacturers should not think of sustainability merely as a box-ticking exercise to appease regulators. Instead, modernization offers an opportunity to increase overall efficiency, minimize waste, and improve margins.
To resolve the apparent conflict between productivity and sustainability, manufacturers can prioritize more than just their final outputs and consider the efficiency of their end-to-end operations. By aligning this with a more ethical operational blueprint, manufacturers can realize how these two goals can act as mutually reinforcing concepts.
The ripple effects of operational efficiency
Sustainability and efficiency, simultaneously.
Perception does not necessarily mirror reality when it comes to how sustainability impacts the manufacturing industry. In past decades, many manufacturers would have been reticent to integrate sustainability-focused initiatives into their wider operations due to the perception that they would negatively impact productivity. Sustainability was equated to stopping production or slowing it down to reduce a carbon footprint or lower emissions.
However, the majority of goals that relate to a more sustainable manufacturing mindset directly mirror the same goals a company would have for improving efficiency. The operational drivers of modern manufacturing have scarcely changed from the days of the Industrial Revolution; manufacturers want to increase productivity, maintain product quality, reduce raw material and resource wastage, save energy, and ensure supply chain resilience. All of which are directly linked to more sustainable operations. By viewing sustainability through the lens of efficiency, manufacturers are not changing their targets, they are simply framing them within a more holistic operational approach, one where sustainability and efficiency are targeted simultaneously.
Our response to regulatory requirements and sustainability objectives don’t need to impede production processes or compel manufacturers to halt their machinery. Instead, change makers can aim to achieve heightened productivity targets through maximally efficient means. To attain enhanced efficiency, manufacturers must first enhance their connectivity, beginning with the integration of processes and operations data. Eliminating siloed environments to guarantee comprehensive visibility, ensures that data is readily available, thereby supporting better decision-making.
If you can’t see it, you can’t improve it.
When it comes to the bottom line, optimized processes lead to cost savings. However, this can only be achieved if data relating to these processes is available, accurate, and accessible to relevant parties. After all, decision makers can’t monitor what they can’t see, and if decisions are being made with incomplete or inaccurate data, the likelihood of an error being made increases dramatically.
Typically, manufacturers have worked despite siloed operations as machines operate independently of one another, but this leads to varied outcomes, disjointed data sets, and an inability to visualize an entire operational set up. The ability to capture data in the right places, interpret it correctly, and then act on it with confidence and accuracy is the very definition of end-to-end visibility.
Controlling what is happening on the factory floor starts with having a full understanding of how all the different machines and processes fit together as part of a cohesive operational system. There is a misconception that end-to-end visibility requires an entire factory floor be on one single platform. This is one way to approach it -- but not the only solution as the data itself can be system agnostic. By compiling this data, from disparate systems, into a single data curation and management layer, manufacturing leaders can find the most suitable version of their own manufacturing modernization.
However, the operational ripple effects also permeate out into the wider ecosystem for enhanced supply chain optimization. Controlling what happens on the factory floor is dependent on what happens outside the factory. This could be the flow of materials into a factory, or the eventual distribution of finished goods to the customers. It is this detailed level of connectivity that is the true holy grail of end-to-end visibility, and it is what drives more sustainable, efficient operations.
Connecting data sources for improved control
The impact unified data has on efficiency.
Since the integration of industrial automation with conventional machinery, manufacturing has moved away from a trial-and-error approach to a data-driven one. The birth of the Industrial Internet of Things (IIoT) opened the floodgates for a whole new level of data collection where every machine, sensor, and device has value as a source of information.
In today’s smart factories, data generation is at an all-time high. This includes everything from real-time metrics relaying machine performance and energy consumption, to metrics that can inform maintenance decisions such as temperature and pressure. But with the sheer amount of data now available, sometimes the full operational picture can become blurred by the granular details.
Standardizing these data sets allows manufacturers to seamlessly integrate data from various sources across an entire smart factory ecosystem. This approach consolidates data from production machinery, IoT devices, inventory and procurement systems, and other relevant sources to ensure a comprehensive view of operations. Relevant information may include everything from tracking real-time machinery output to monitoring environmental variables such as temperature and humidity in order to optimize production conditions. Such integration establishes a cohesive data foundation, facilitating real-time insights and informed decision-making, thereby inherently embedding continuous efficiency benefits into the process.
The impact unified data has on sustainability
The benefits of real-time data visibility apply to both flexibility and sustainability. In legacy factories data typically exists in isolated towers or silos which remain unconnected. Having visibility and insights into what is happening in all areas of a business allows the creation of a more complete operational picture.
When everything is connected and relevant data is made visible, manufacturers will be able to develop strategies – rooted in accurate data – which are aimed at eliminating unnecessary waste, reducing complexity, and making operations safer. All of this ties into the broader goal of enabling more sustainable and efficient manufacturing operations.
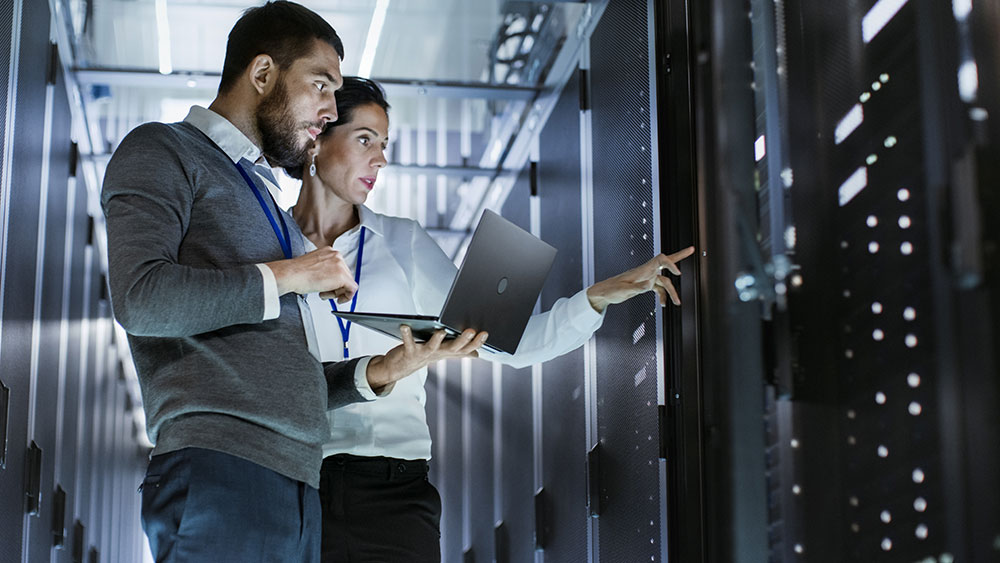
Connecting data for Smart Factories: Optimizing control and sustainability.
Setting sustainable targets
Manufacturers are under mounting pressure from customers and stakeholders to develop more sustainable business practices. Therefore, there is an inherent need to align strategies with these goals and ensure that any investments yield optimal outcomes.
But these goals need to be oriented around specific targets whereby KPIs or outcomes are not just another box to be ticked. Otherwise, what may look like greener, more sustainable operations - reducing idle time as an example - becomes a system to be gamed and manipulated.
In such instances, managers may simply slow down production processes to give the perception of sustainability and efficiency targets being reached. If companies really want to make an impact on carbon reduction and sustainable growth, data needs to be aggregated and analyzed constantly, amidst the rise of mandatory sustainability reporting requirements advancing across the globe. The SEC press release regarding new rules for standardized climate-related disclosures being a particularly recent example.
This proactive approach to data collection also mitigates the risk of fines and reputational loss that comes from non-compliance. As a result, manufacturers will always be on the front foot when it comes to accurate reporting and conforming with changing regulations.
Increasing quality standards
Taking control
To maximize the benefits of utilizing IoT and AI, quality assurance needs to be maintained. By effectively using unified data alongside machine learning algorithms and AI-driven solutions, businesses can achieve a higher level of quality assurance than would otherwise be possible through conventional methods.
This could be using high-accuracy AI modeling to consistently produce the required quality of mass-produced components, or the development of quality assurance systems that can identify possible defects in raw materials before goods are produced. One example of this approach in action is Fujitsu’s collaboration with SUBARU to develop an AI system that heightens the accuracy of camshaft grinding and enables optimum camshaft quality without requiring manual inspection.
Through continuous monitoring and verification of the AI predication models alongside quality inspection results, degradation of AI modeling accuracy is prevented. Operators can therefore re-tune models in real time. When manufacturing and evaluation is conducted simultaneously, faulty components or discrepancies can be quickly identified and removed to prevent disruptions.
This technological leap ensures products continue to meet stringent quality standards, boosting efficiency and consumer trust while diminishing the risk of costly recalls or reputational damage. The sustainability benefits of increased quality control also mean less waste, fewer returned goods, and improved overall consistency; all of which reduce environmental impact.
Solve efficiency problems first to realize sustainability gains
Often when it comes balancing productivity and sustainability, the problem is solved by targeting machine efficiency. Changes that look to eliminate waste in raw materials and energy usage, will bolster productivity without increasing carbon footprints. Coincidentally, this ties directly to some of the United Nations Sustainable Development Goals, especially regarding responsible consumption and production.
By selecting key areas of investment based on desired goals, costs, and potential returns, all of which will naturally lead to sustainability gains, manufacturers can harness revolutionary digital solutions to solve efficiency problems.
As an experienced innovator in manufacturing solutions, Fujitsu offers a variety of solutions – including the Digital Annealer, which helps solve complex optimization issues using a quantum-inspired approach. This solution provides unified insights ranging from refining factory logistics to amplifying supply chain proficiency, all of which can lead to efficiency and sustainability benefits. The Fujitsu Kozuchi platform also exemplifies AI's transformative role for manufacturing operations by integrating with factory systems, using digital twins, advanced visualizations, and simulations, to deploy advanced AI algorithms.
Now manufacturers can enable data-driven, agile operations that target production capacity increases and plant modernization, highlighting the transformational ways that digital solutions can support both operational efficiency and productivity in manufacturing simultaneously.
Conclusion – Enabling greater data visibility
Without a digital foundation on which to leverage efficiency gains, sustainability initiatives risk becoming akin to greenwashing. Improving operational efficiency and sustainability requires the dedication of resources towards digital solutions that support data collection, unification, and analysis.
By embracing smart manufacturing technologies, factories can increase operational efficiency and agility. But first, sustainable manufacturing operations start with efficiency gains and an environment where smarter choices can be made quickly in continually changing conditions.
With the right data insights and smart manufacturing technologies in place – all of which Fujitsu can offer - manufacturers can increase manufacturing efficiency and uncover productivity gains, while also progressing towards crucial net-zero targets.
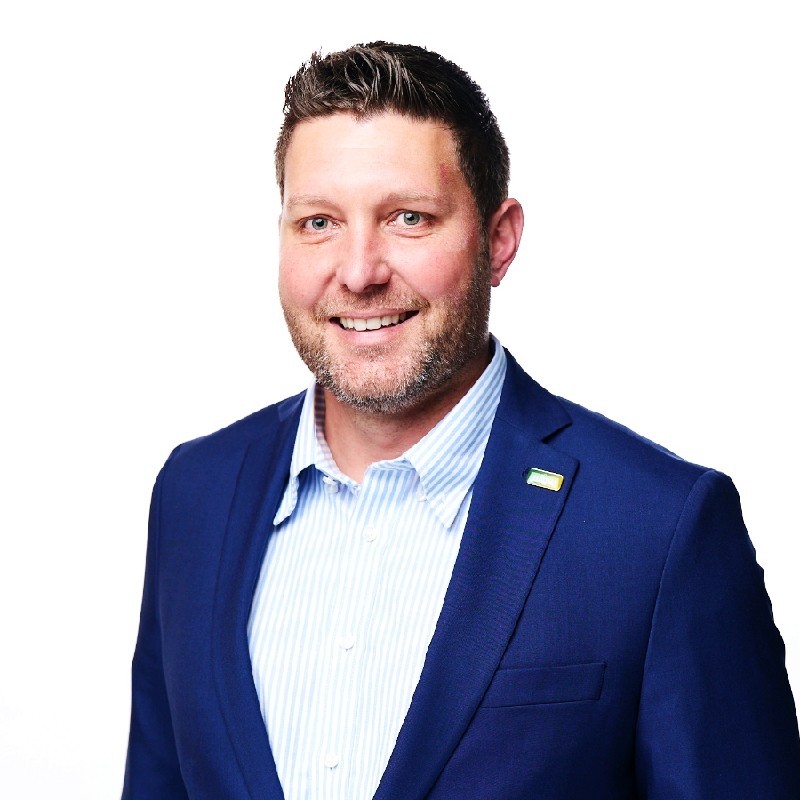
Johan’s overall focus has been on the digital enablement and automation of key manufacturing capabilities and ability to drive compelling value to Fujitsu clients.
Editor's Picks
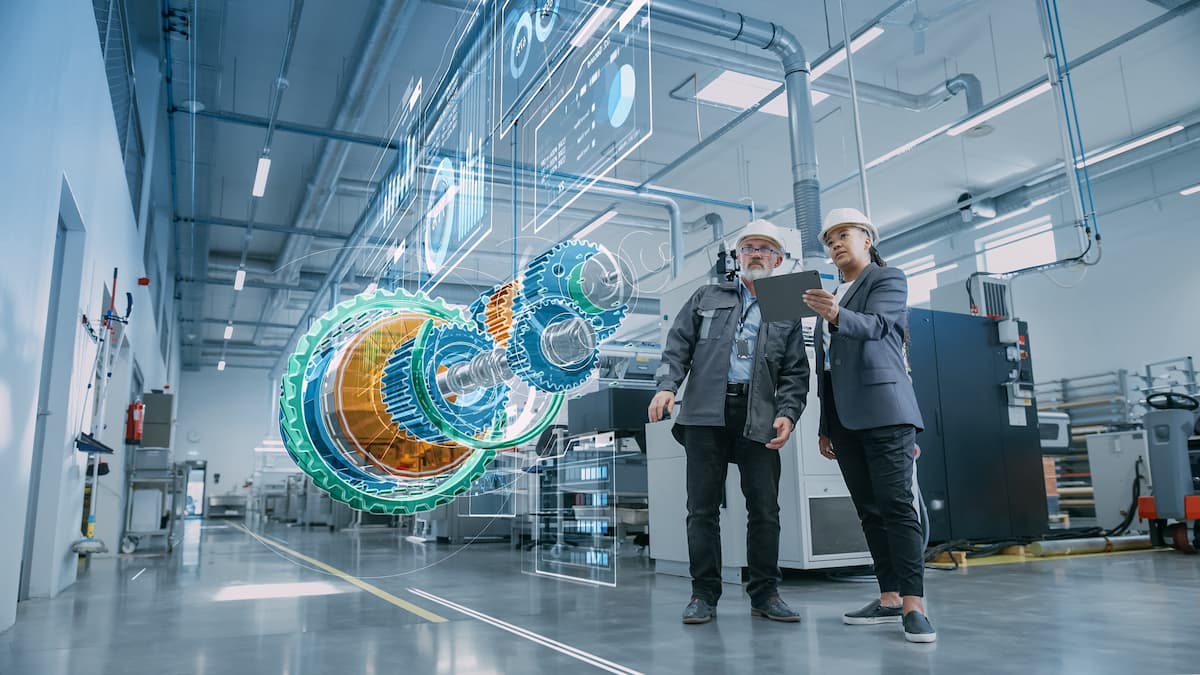
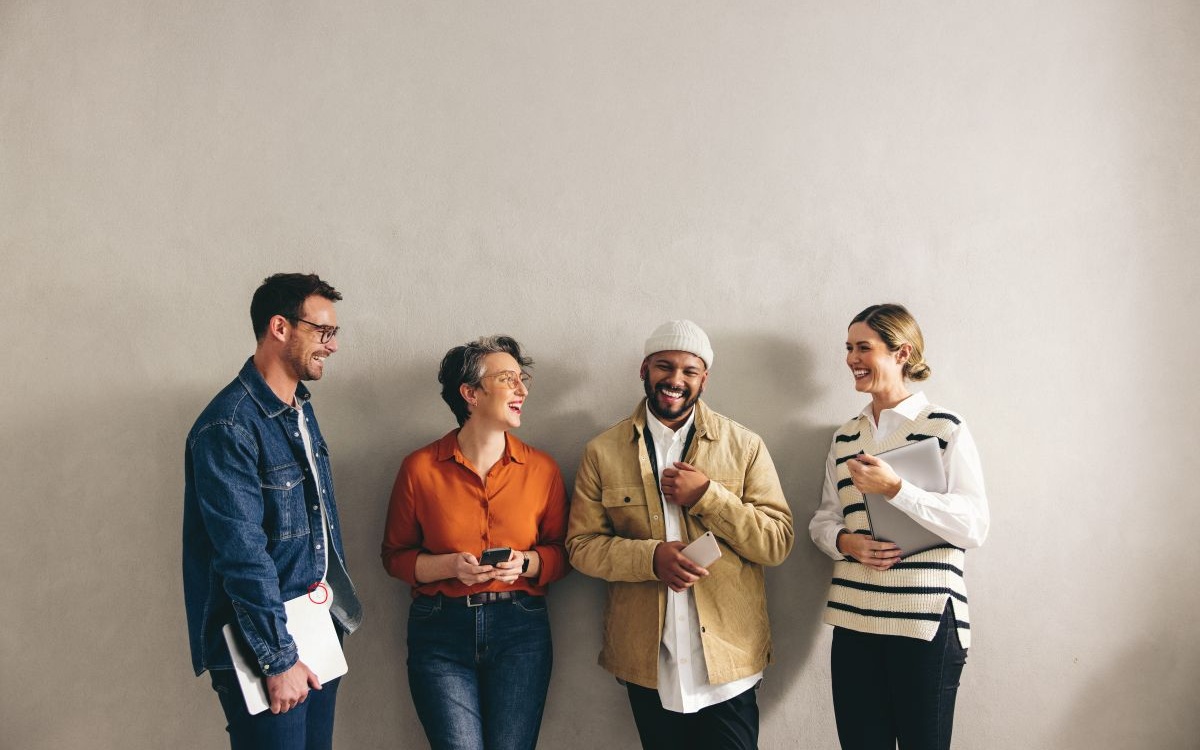
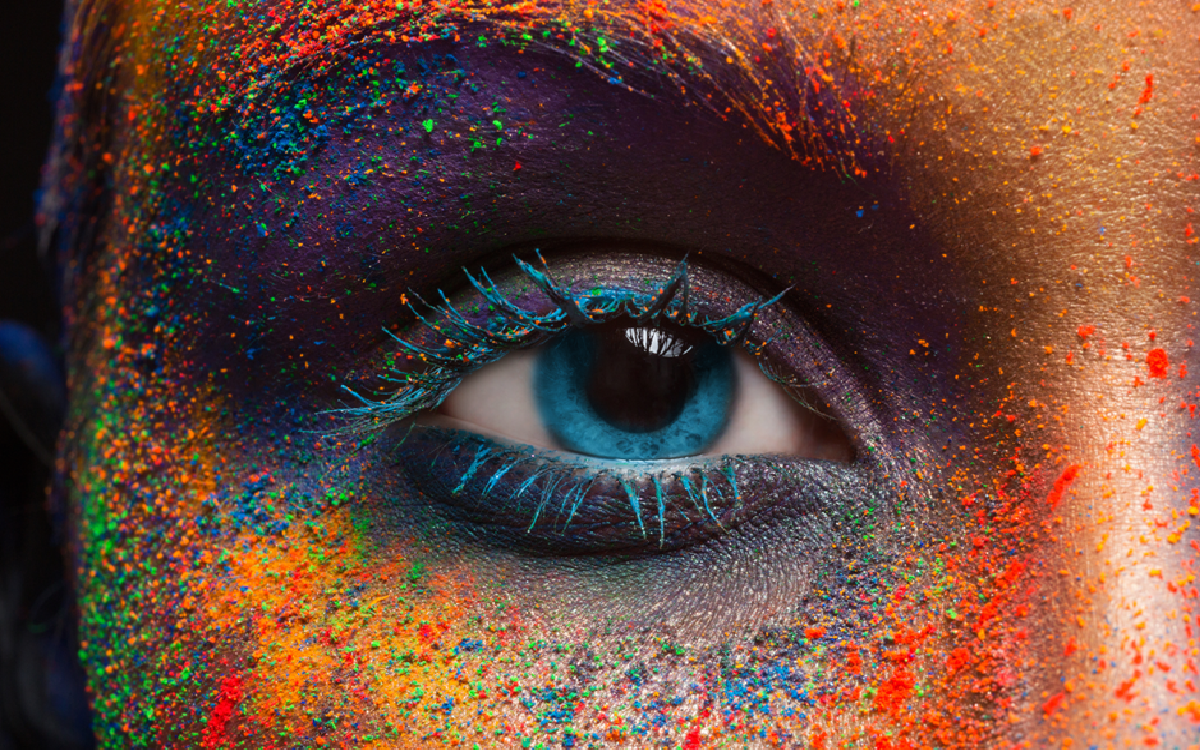