Making factory operations sustainable with AI-powered monitoring
Fujitsu / March 27, 2024
In today's rapidly evolving industrial landscape, manufacturing businesses are grappling with a myriad of challenges. Among these, the existence of silos and inefficiencies stand out as significant hurdles. These issues not only hamper productivity and profitability but also contribute to a higher carbon footprint. As industries continue to expand and evolve, the environmental impact of their operations is becoming increasingly evident. This has led to a growing recognition of the urgent need for Sustainability Transformation.
In this blog, we delve deeper into the challenges of factory silos and inefficiencies, explore their impact on the carbon footprint, and discuss the steps that businesses can take to embark on a Sustainability Transformation by using Artificial Intelligence (AI).
Sustainability Transformation of factory operations
The concept of Sustainability Transformation goes beyond mere compliance with environmental regulations. It involves a fundamental shift in the way businesses operate, with a focus on reducing waste, improving efficiency, and minimizing the environmental impact of their operations. This transformation is not just about doing the right thing for the environment; it also makes good business sense. Companies that embrace sustainability often find that they can reduce costs, improve their brand image, and attract a new generation of environmentally conscious consumers.
However, achieving Sustainability Transformation is no easy task. It requires a comprehensive and strategic approach that addresses the root causes of inefficiency and environmental impact. This includes breaking down silos, improving processes, and investing in new technologies and practices that promote sustainability.
The environmental footprint of inefficiencies
Many manufacturing organizations often suffer from unplanned interruptions to production, due to an unstable IT / OT environment. Such factory outages can lead to waste of raw materials that were being processed when the systems failed. The energy used to restart the machines leads to unnecessarily higher energy consumption. Additionally, there could be equipment damage, cleaning costs, wasted working hours, and in extreme cases, unintended release of chemical waste into the environment. All these scenarios increase the factory’s environmental footprint.
Another source of increased carbon footprint is inefficient use of servers, storage and IT resources in general. Without a clear, transparent picture of application landscapes, resource consumption is often very inefficient resulting in more IT investment than is actually being consumed. This results in higher energy consumption, increased use of resources for cooling, and greater e-waste.
Root causes of unstable IT/OT environments
In multi-vendor factory environments, the systems’ responsibilities and related resource monitoring solutions are often siloed. This can lead to complex troubleshooting cases, where the dependencies between different systems or application components are not known. With various permutations of components’ dependencies, this can lead to difficulties in finding root causes of each incident. Resolution across multiple vendors also becomes difficult without clarity and transparency on source of the problem. All of these factors result in an unstable IT/OT setting, with siloed approaches and inefficiencies, leading to a higher carbon footprint and environmental damage.
How can AI help with sustainable factory operations?
AI has emerged as a powerful tool that can enable comprehensive monitoring and observation in factory operations, and help reduce inefficiencies, thereby playing a pivotal role in Sustainability Transformation.
AI can help break down silos by facilitating seamless communication and data sharing across different departments and teams. This can significantly improve operational efficiency and reduce waste. For instance, AI-powered predictive analytics can forecast production needs accurately, thereby minimizing overproduction and reducing resource wastage. Moreover, AI can also help in real-time monitoring of factory operations. It can track energy consumption, waste production, and other key sustainability metrics, providing valuable insights that can guide decision-making. For example, AI algorithms can analyze energy usage patterns and identify areas where energy consumption can be reduced.
AI can also play a crucial role in predictive maintenance. By predicting equipment failures before they occur, it can prevent costly downtime and reduce the environmental impact of manufacturing operations. This not only saves money but also reduces the carbon footprint of the factory. Furthermore, AI can facilitate the transition to a circular economy, a key aspect of sustainability. It can help in tracking and managing resources throughout their lifecycle, promoting recycling and reuse, and minimizing waste.
What are the low hanging fruits to start immediately?
As part of the Fujitsu Sustainable Manufacturing Digital Factory offering, the Factory IT Monitoring Operations Center (MOC), is a solution available today that consolidates the monitoring of various third-party services, factory infrastructure, and applications into a single AI-powered platform.
The MOC unites existing silo-based views into a single pane of glass. With this consolidated data, AI is used to automatically create a topology mapping of all the components’ dependencies and generate an automatic root-cause analysis for each incident. With full-stack visibility to the server and application landscapes, resource consumption can be optimized based on the comprehensively monitored insights. All of this ensures better system stability and faster mean-time-to-recovery (MTTR).
This also results in a change in perspective from “reactive” to “pro-active” operations, promotes transparency and cooperation between multiple vendors and stakeholders, and facilitates distraction-free manufacturing operations. With increased stability and uptime of critical systems in the IT/OT environment and a marked reduction of production outages, manufacturing organizations can break down silos, significantly reduce inefficiencies, and minimize their carbon footprint.
Conclusion
Sustainability Transformation of multi-vendor, factory environments is complex, but with by leveraging data and key technologies such as AI, manufacturers can not only achieve their sustainability goals but also improve operational efficiency and profitability. Fujitsu Uvance Digital Factory is an initiative to not only help solve business transformation challenges, but also work together with manufacturing organizations to help save the environment. Together, we can co-create an environmentally responsible future of manufacturing. The best first step might just be to talk to us. https://www.fujitsu.com/global/contact/
In the interim, if you want to explore an AI toolkit, feel free to check out Fujitsu Kozuchi - a cloud-based platform structured around 7 key areas of AI, enabling rapid development, testing, and implementation for immediate business results. www.fujitsu.com/global/kozuchi.
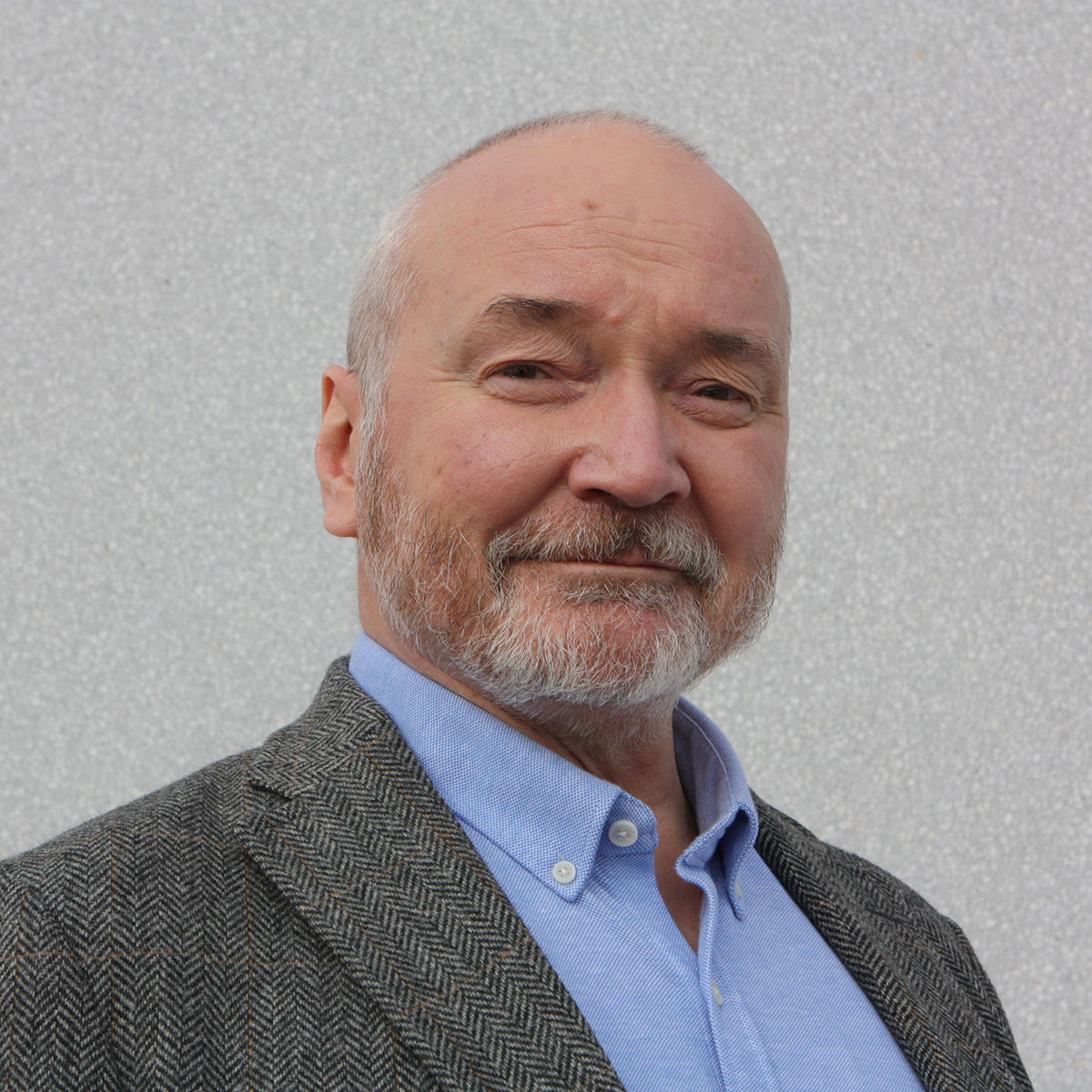
Related information
Editor's Picks
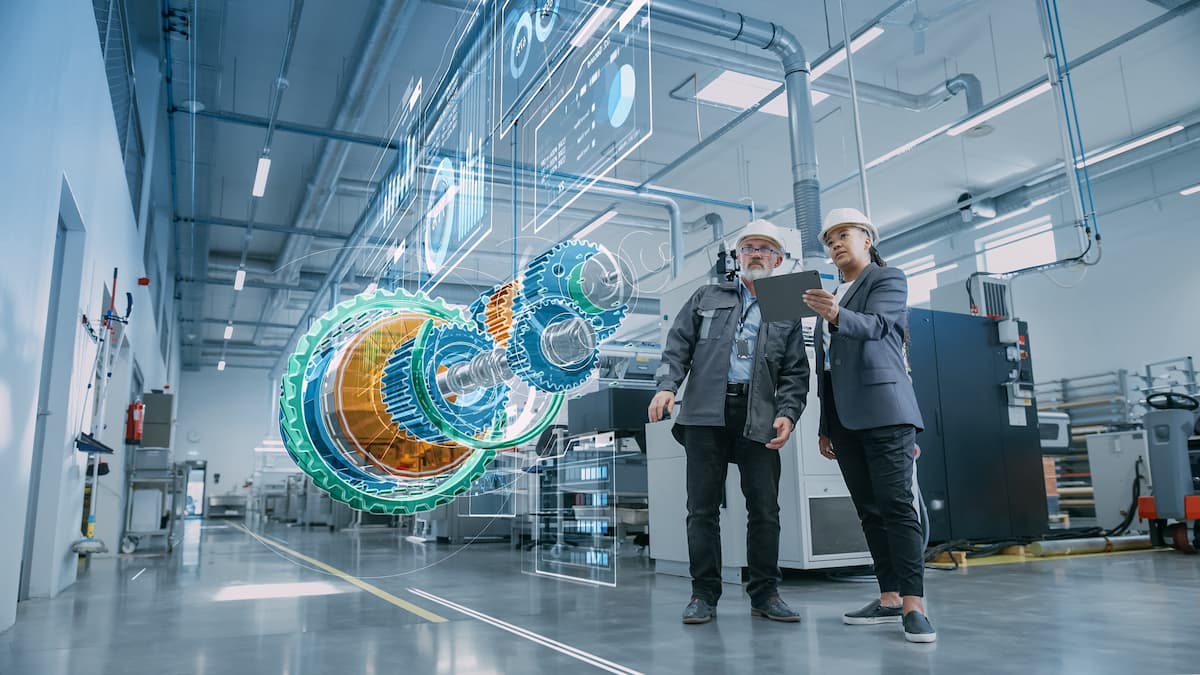
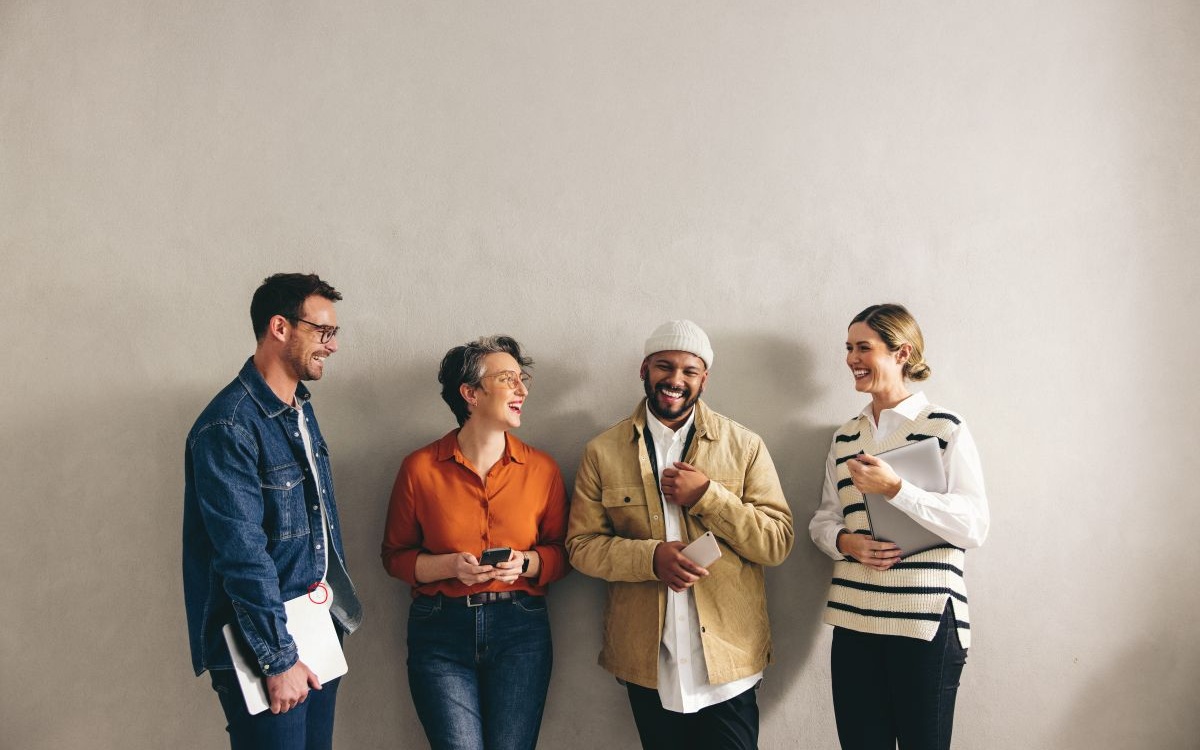
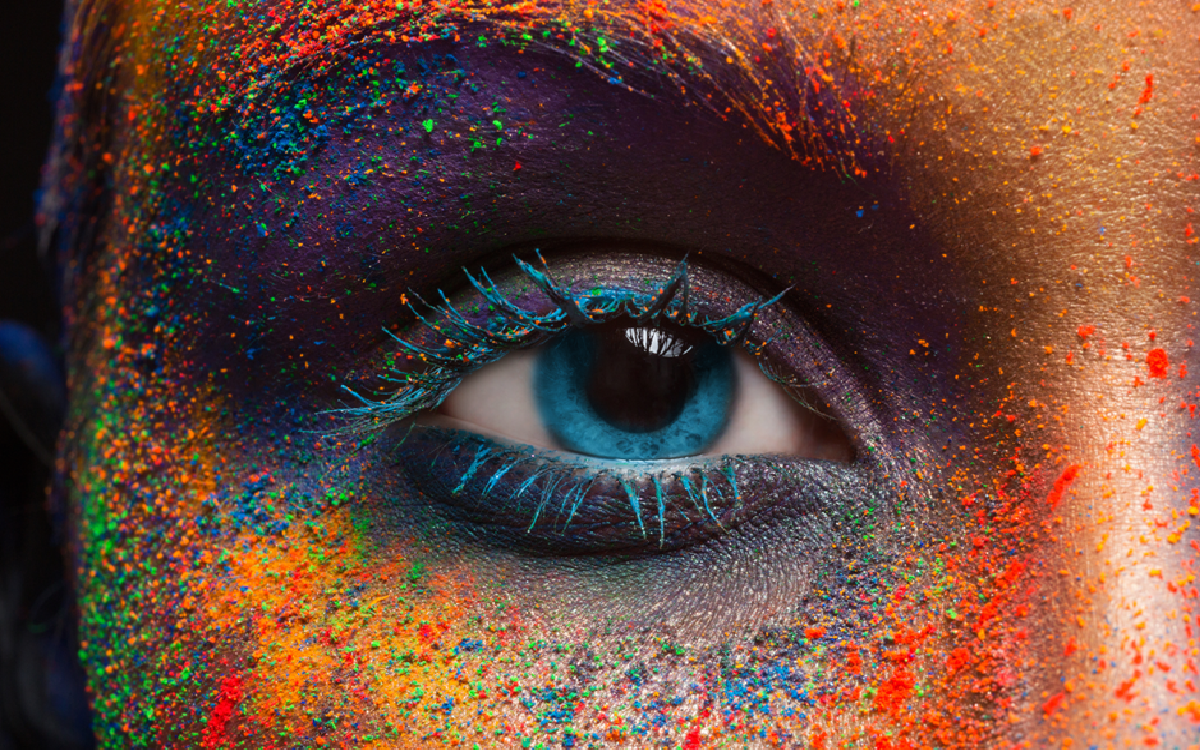