Boosting operational resilience and sustainability with Proactive Factory Management
Fujitsu / November 27, 2024
In today's manufacturing landscape, organizations face an increasingly complex balancing act: the need to drive profitability while simultaneously reducing environmental impact. As pressure mounts from consumers, regulators, and stakeholders to adopt more sustainable practices, manufacturers must find innovative ways to meet these seemingly contradictory goals.
The majority (70%) of executives say SX is a top priority, but only 26% of organizations report tangible results from their sustainability strategies.
Within the current rapidly evolving industrial environment, traditional reactive approaches to concepts such as maintenance, where problems are addressed only after they arise, are no longer sufficient.
Proactive Factory Management presents a transformative approach that leverages advanced technologies and data-driven insights to revolutionize manufacturing operations. By embracing the principles of Smart Manufacturing and Industry 4.0, organizations can improve Overall Equipment Effectiveness (OEE), minimize their environmental footprint, and boost profitability, all while staying ahead in an increasingly competitive market.
Macroeconomic factors and production lines running at higher capacity now mean that an hour of unplanned downtime costs manufacturers at least 50% more than five years ago.
The dual pillars of Proactive Factory Management
At its core, Proactive Factory Management rests on two fundamental pillars: equipment monitoring and operational security. Together, these elements form the foundation for optimized manufacturing processes that drive both efficiency and sustainability.
Monitoring equipment for uptime and efficiency
The proactive management of physical equipment and processes has become essential for maintaining smooth operations and preventing costly downtime.
Manufacturing downtime can cost up to $400,000 per day when production lines are not running, highlighting the critical importance of preventive measures.
Consider the example of palletizers, where AI vision systems can identify subtle misalignments and provide early warning signs that components like brakes are wearing out. By detecting these minor issues before they escalate, manufacturers can prevent major breakdowns, ensuring continuous operation, and maintaining product quality throughout the supply chain.
Securing operational technology for continuous production
Operational Technology (OT) security plays a vital role in preventing disruptions caused by both malicious attacks and unintentional errors. Well planned OT ensures the integrity and reliability of manufacturing systems, allowing businesses to focus on their sustainable production goals without the constant threat of interruption.
For instance, intelligent monitoring systems can detect and rectify incorrect data input by operators in real-time, preventing unnecessary machine shutdowns. This level of vigilance goes beyond mere cost savings, ensuring an optimized process through proactive maintenance and management.
Key building blocks for success
Standardization and connectivity
One of the major challenges facing manufacturers with legacy systems is the lack of standardization across factory operations. When disparate systems have developed over decades, performing regular updates, patches, or backups becomes increasingly difficult.
Proactive Factory Management addresses this challenge head-on by integrating IoT and digital technologies that standardize operations and offer real-time insights. But for these goals to be achieved - real-time collaboration, instant data access, and unified communications – connectivity is critical.
5G/6G networks that enable real-time feedback, instant process adjustments, and seamless operations with minimal delay can help manufacturers unlock the full potential of IoT, integrating sensors, machines, and systems into a unified operational structure. Now, the once separate worlds of IT and OT can be more easily connected. This creates a smooth flow of data from the shop floor to the executive level for agile decision-making, enabling adaptive, predictive, and continually optimized manufacturing processes.
This standardized level of enhanced connectivity enables comprehensive monitoring, allowing manufacturers to:
• Track operational data in real time
• Perform predictive maintenance
• Anticipate problems rather than react to them
• Standardize processes across multiple facilities
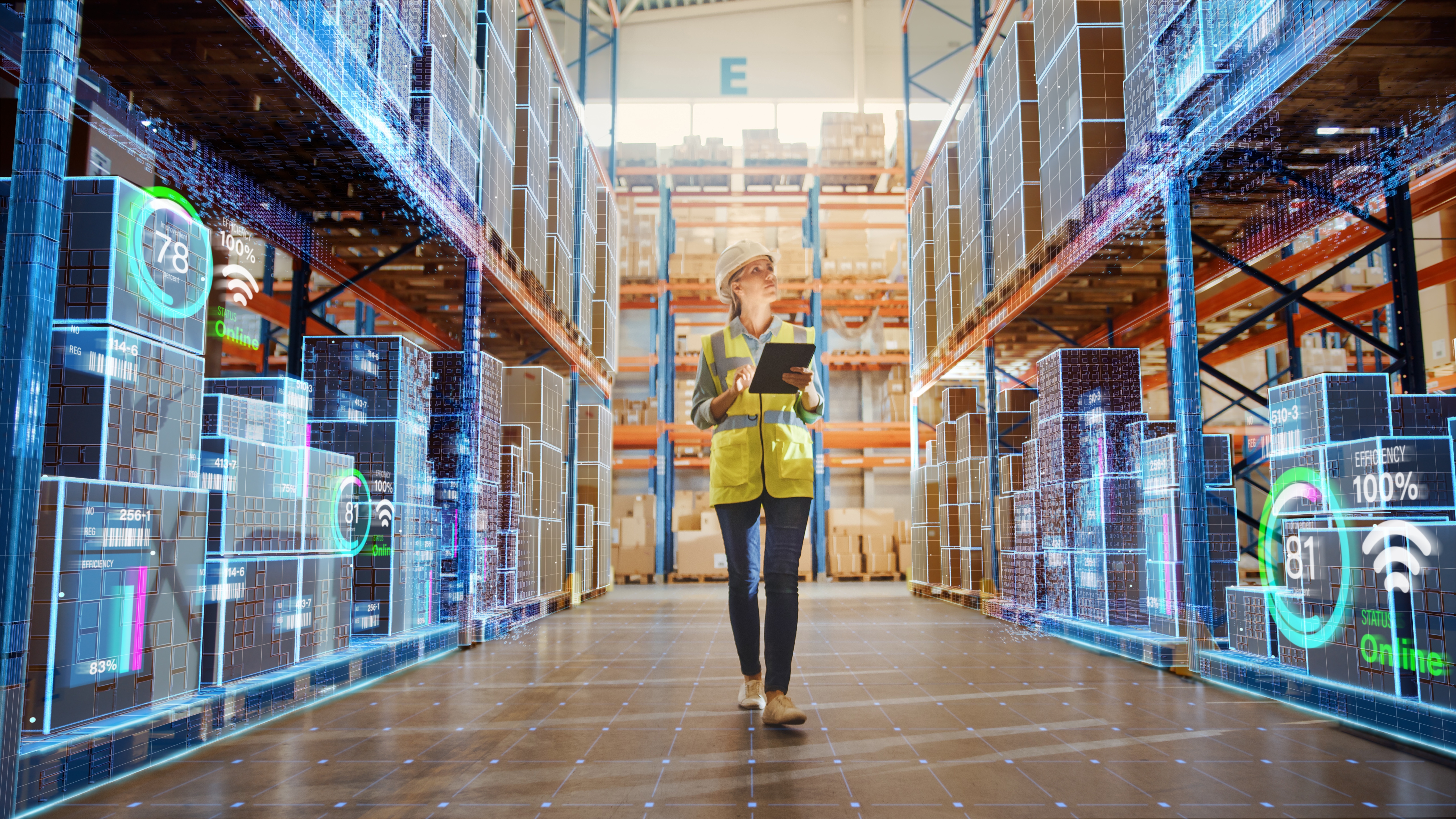
AI-powered monitoring
AI vision technology serves as a cornerstone of Proactive Factory Management, allowing manufacturers to observe processes that may be difficult to monitor manually. These advanced systems can:
• Assess the quality of raw materials upon arrival
• Detect unwanted materials in the production line
• Predict the efficiency of downstream processes
By proactively adjusting operations based on AI insights, manufacturers can reduce waste and optimize energy consumption, all of which minimizes environmental impact while ensuring consistent product quality.
Predictive maintenance
Proactive Factory Management excels in anticipating equipment failures before they occur, optimizing spare parts inventory and reducing unplanned downtime. This predictive approach enables a powerful data-driven feedback loop with suppliers which follows a repeatable pattern:
1. Monitor wear patterns of critical components
2. Identify recurring issues more effectively
3. Provide actionable feedback to suppliers
4. Rectify component issues at the source
A bearing within a machine consistently fails after 500 hours despite being rated for 1,000. Manufacturers and engineers notice the data signaling this and reach out to the suppliers to flag this issue. The supplier can then determine how and why this is happening, improving the quality of the bearing they are producing. This then improves the overall component quality as well as the OEE for the manufacturer due to less downtime, reducing the wasted resources and labor that comes with repeatedly having to change one faulty part.
The sustainability impact
Proactive Factory Management directly supports sustainability goals by minimizing resource waste and optimizing energy consumption. When machines operate at peak efficiency, they not only reduce unnecessary energy use but also eliminate downtime that could result in product or material waste.
Here, the circular economy can be realized. Instead of the traditional linear model—produce, use, and discard—the circular economy within manufacturing focuses on keeping materials in use for as long as possible through processes like remanufacturing, recycling, and upcycling.
Smart manufacturing enhances this approach by using real-time data to optimize production processes, predict maintenance needs, and reduce material waste. It also enables closed-loop systems, where by-products or waste are repurposed into the manufacturing cycle, lowering environmental impact and fostering sustainable production.
It encourages producers to maximize the value of by-products, identifying and capitalizing on potential revenue streams from waste materials implementing closed-loop systems for resource reuse. Can excess heat or energy be sold for other industrial uses? Can waste products be utilized in other business areas? Answering these questions is how manufacturers can create a closed-loop system that supports environmental goals and bottom-line targets.
But this only comes from having the data and the visibility of broader manufacturing operations. Having this level of granular visibility allows factories to plan ahead, ensuring that operations are not just consistent, but align with sustainability targets through minimizing last-minute emergency shipments that can increase the carbon footprint.
Success story: A leading UK food producer leveraged AI vision to accurately assess raw material quality upon arrival. This allowed them to adjust chemical and energy usage precisely, reducing their environmental footprint. During the process of converting raw resource into final product, they were also able to repurpose by-products detected during these assessments into sellable materials like soil enhancers and animal feed.
The future of factory management – the industrial metaverse and AI-driven operations
The industrial metaverse: virtualizing the factory for total control
The future of proactive factory management lies in the complete virtualization of the factory through the industrial metaverse. This cutting-edge development enables manufacturers to visualize and manage every aspect of their operations in a fully immersive digital environment. Whether you’re monitoring production lines from your control room, checking machine health from a tablet, or interacting with factory systems via AR glasses, the entire factory becomes accessible from anywhere in the world.
By creating digital twins of physical assets, manufacturers can not only see what’s happening on the shop floor in real-time but also make instant adjustments. For instance, if AI detects a slight deviation in a machine's performance, you can simply issue a verbal command or click a button to correct the issue. This seamless integration of the physical and digital worlds enhances visibility, responsiveness, and operational precision.
AI takes the lead: managing factories with unprecedented precision
Looking ahead, the role of AI in factory management is set to expand dramatically. Today, AI systems already support predictive maintenance and real-time adjustments, but the future will see AI taking full control of the manufacturing environment. AI will not just provide recommendations—it will run the entire factory autonomously, making data-driven decisions faster and more accurately than human operators.
Imagine a factory where AI monitors millions of data points every second, predicting potential failures long before they happen, optimizing energy usage, and responsively adjusting production processes. It will notify you of changes it makes—such as reducing the load on a conveyor belt to extend the life of a critical component—but the decision-making will be instantaneous and fully automated. This shift represents a leap of faith for manufacturers, trusting AI to make better operational decisions, but the results will be undeniable: increased efficiency, zero downtime, and lower environmental impact.
Conclusion - Embracing a smarter, greener future with AI and virtualization
As we embrace these technologies, the future of factory management will not only be about efficiency but also about sustainability. AI-driven factories will use resources more intelligently, cutting down on waste and energy consumption by continuously fine-tuning every aspect of the production process. The industrial metaverse will allow companies to test changes in a virtual environment before implementing them in the real world, reducing the risk of disruptions and ensuring the most sustainable practices are adopted.
In this AI-powered future, manufacturers will have the ability to scale operations seamlessly, all while meeting increasingly stringent sustainability standards. The fusion of AI, the industrial metaverse, and proactive management will create a manufacturing ecosystem that is self-optimizing, sustainable, and resilient.
As these technologies evolve, the role of human operators will shift from hands-on management to overseeing AI systems, enhancing collaboration between human intelligence and artificial intelligence. The future of factory management is not just about reacting faster—it’s about staying ahead of the curve, reducing environmental impact, and driving continuous innovation in a smart, sustainable world.
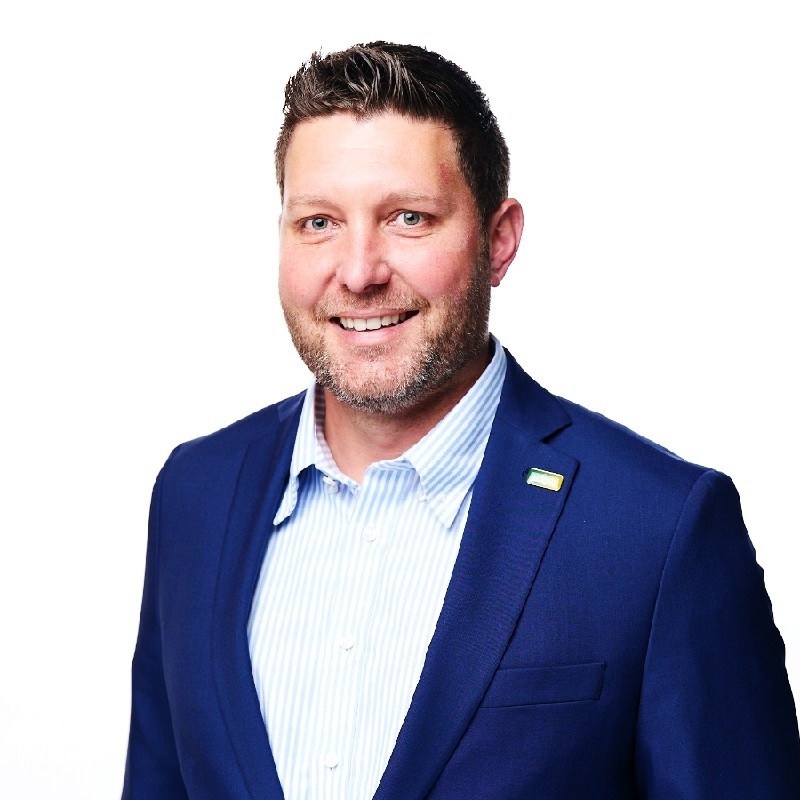
Editor's Picks
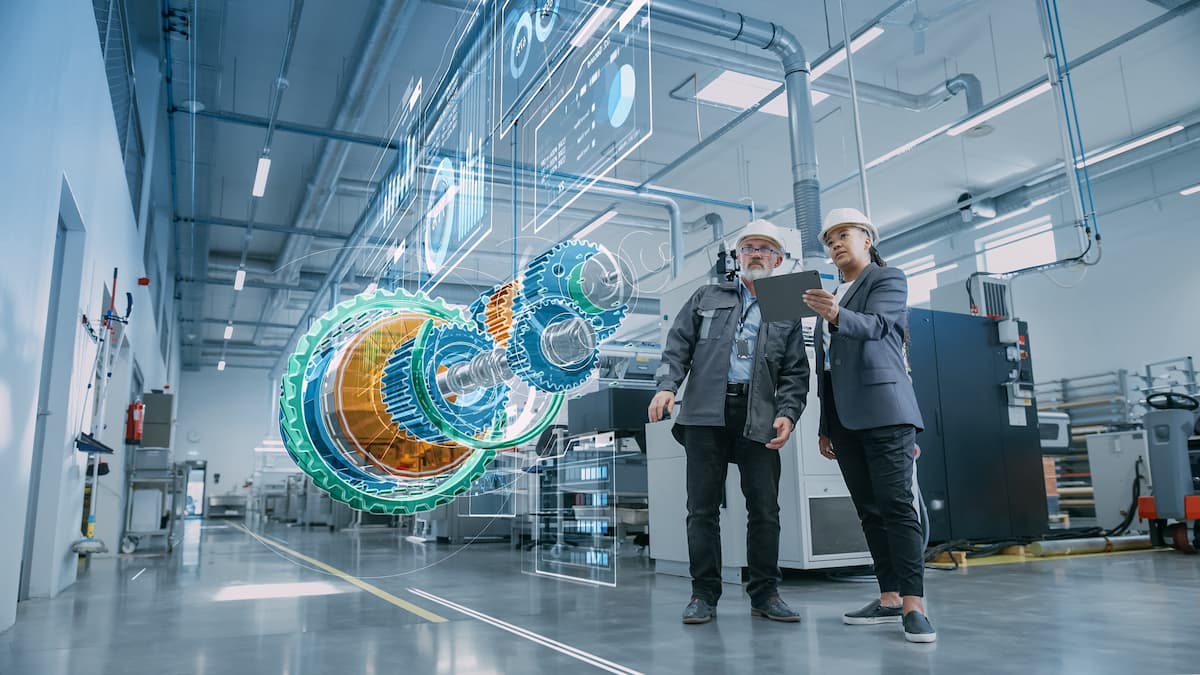
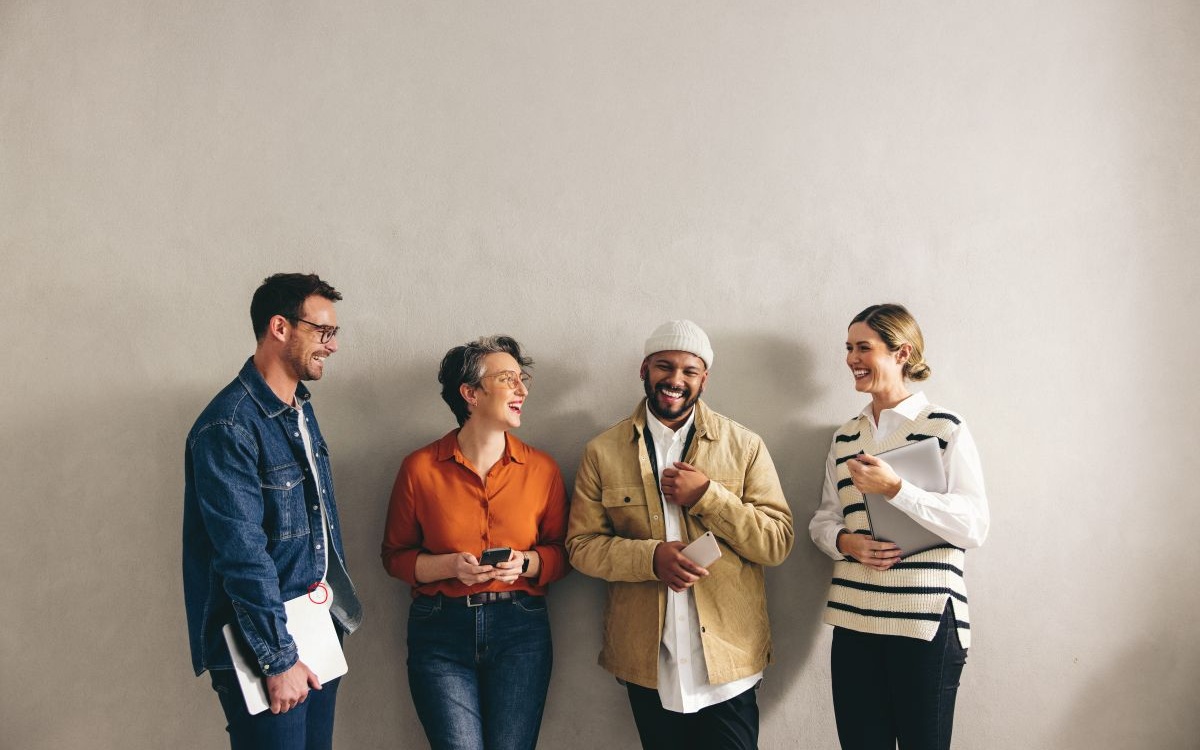
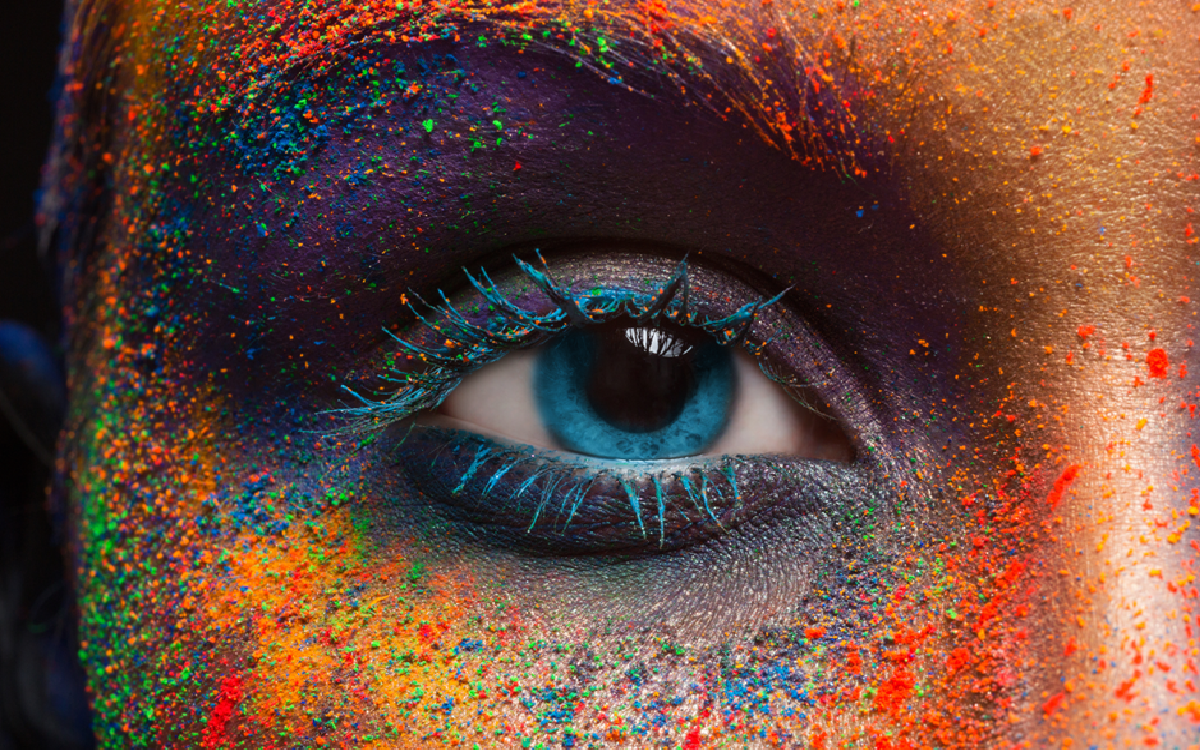