Next-gen manufacturing: Perpetuating sustainability and efficiency through innovation
Fujitsu / January 11, 2024
The manufacturing industry has been through many different phases of evolution, each of which has contributed to increasing levels of productivity.
However, there is one constant theme that connects each phase of manufacturing innovation: the introduction of new technology. From the cotton gin to industrial conveyer belts, mainframe computers to tablets, to robotic augmentation on assembly lines, the pattern is clear — exploring the frontier of technology is a prerequisite to growth.
In today’s factories, this is more important than ever before. We have all seen the news of how pandemics, natural disasters, wars, and even cyber-attacks are able to bring entire operations to a halt.
But where there are challenges, technology provides solutions. With industrial technology advancing at a faster and faster rate next-gen technologies such as AI, ML, digital twins, and the industrial metaverse – are providing answers to the age-old manufacturing conundrum: how can you safely and responsibly produce more with less?
The role of AI for analysis in manufacturing
AI has emerged as a transformative technology across various industries, including manufacturing. In recent years, AI has played a pivotal role in revolutionizing manufacturing processes, optimizing efficiency, and driving innovation.
Converging the power of AI-based capabilities, such as machine learning and robotics, creates the potential to reshape existing manufacturing methods and propel companies into a new era of intelligent automation.
The data-driven generation
Manufacturers have always sought technical data, but typically this has skewed towards focusing on the past, rather than instilling a proactive mindset. Now, with AI systems and advanced data processing capabilities, not only is the quality of data more robust, but it enables much quicker, accurate decision-making to take place with limited human input.
AI can shine a light on the most valuable data by interconnecting multiple large data sets into a single mega-data landscape, and then analyzing that data faster and with more efficiency than prior technologies. This capacity to bring focus to the data not only simplifies the overall decision-making process, but it also reduces the opportunity for human error. However, responsibly designed AI is not a static solution. With each data set that it analyses, it will learn and optimize over time, so iteratively each operational process it is applied to will become more and more effective.
Real-time, real impacts
This real-time aspect to AI is where manufacturers can embrace flexible automation. Where a human may take hours or days to react to a data point or stimulus, AI can prompt a repair or corrective action in an instant. Sensors and connected devices (IoT) on the ‘shop floor’ enable this kind of quick action, but they also generate huge amounts of data. To make the most of the IoT investment, AI can be used to responsibly analyze both structured and unstructured data at scale, deriving real-time insights to deliver real-time impact.
More conventional technologies like MES platforms also now seamlessly integrate the physical with the digital, leveraging AI-assisted analysis to monitor equipment, and pre-empt disruptions before they happen. This ability to instantly react to data ensures rapid responses that reduce machine downtime and positively impact overall product quality.
Data-driven management
Supported by AI capabilities, manufacturers can now plan with a much greater level of accuracy. This applies to both internal plant operations, using capabilities such as predictive maintenance, and to external factors, such as identifying potential supply chain disruptions.
Integrating AI into manufacturing operations provides significant advantages in predictive maintenance. By learning from historical data sets and analyzing sensor data, AI can predict when a machine is likely to fail or need maintenance. No longer do manufacturers have to wait for a machine to require a service, or for it break down entirely before working on it. Instead, a pre-emptive approach allows companies to avoid costly downtime and extend the life of their equipment, both reducing waste and boosting productivity.
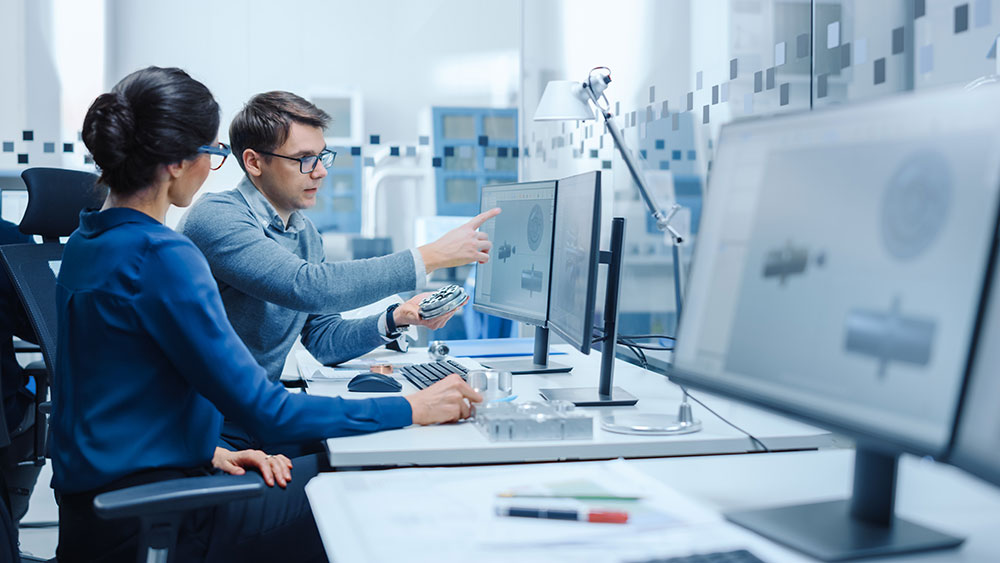
AI boosts manufacturing: Preventing downtime, enhancing productivity with predictive maintenance
Additionally, AI can be used to enhance supply chain decision making. Predictive analytics can help anticipate demand patterns and optimize inventory management. Even more advanced forecasting technologies can predict weather patterns to anticipate raw materials shortages or to adjust production schedules in advance of severe weather events.
The role of next-gen technology for the workforce
But innovation is not about replacing people. Technology solutions need to work with people not against them. Although technology is an important pillar of organizations’ competitiveness, people remain essential to factory operations. Manufacturing is more than a sum of subtasks that can simply be handed over to robots and left alone in perpetuity. Human workers are needed to control, troubleshoot, and execute increasingly complex operations.
Improved safety through next-gen solutions
In manufacturing, workplace safety is a main priority. Virtual Reality (VR) and Augmented Reality (AR) solutions create a platform to safely and consistently limit worker exposure to hazardous situations, without compromising productivity.
Without question, many traditional manufacturing jobs are physically demanding. They involve lifting, carrying, and moving heavy items and can require interacting with hazardous materials and potentially dangerous machinery. These conditions are a deterrent in recruiting new workers. However, advanced technologies can overcome these physically demanding workplace conditions. Augmentation advancements such as the use of exoskeletons or cobots aim to protect employees’ health, allowing them to perform tasks safely.
VR and AR also paves the way for better hazard perception and accuracy in operations by providing workers with viewable 3D work instructions and information specific to the product and processes, while tailored to the workers’ skill level. Even operational design is enhanced with virtual reality. Through VR-supported layout planning and accurate 3D human models, manufacturers can balance workforce safety and productivity by virtually simulating their operations to swiftly gain insight into a decision’s impact, and then advising on the best course of action.
Digital twins for training
Human-machine collaboration is becoming increasingly prevalent in manufacturing settings, with staff interfacing with AI systems through voice commands or wearable devices. But there is an additional benefit that next-gen technology offers a workforce – the ability to develop and upskill abilities.
Augmented technologies enable an engaging platform for lifelong learning and development. Digital twin simulations can accurately visualize industrial processes, while AR and VR supports training with mobile learning and smart workstations enhancing on-the-job learning.
Upskilling is therefore made easier due to more accurate and engaging training on a digital twin. At the same time, manufacturers will benefit from enabling immersive experiences where teams in different locations can collaborate in the same VR session for training or safety planning purposes.
Digital replicas of plant operations are often implemented for their use in refining process and improving productivity. But they are also fertile ground for growing an engaging and effective worker training program.
The role of the industrial metaverse
Combining AR and VR technology, with massive IoT datasets and AI creates the industrial metaverse. This is the next ‘next-gen’ technology that will likely see widespread usage on the factory floor. It has the potential to revolutionize the way companies operate, providing new opportunities for optimization, innovation, sustainability, and growth.
Visualizing the invisible
The industrial metaverse offers ground-breaking tools for functional plant design and optimization, allowing users to make immediate operational changes. By digitally replicating physical assets in real-time, manufacturers can swiftly react to and orchestrate operations, revolutionizing facility coordination, and ensuring a seamless manufacturing landscape.
Organizations can now simulate products, machines, and even entire factories in the metaverse. Newer technologies and computing power enable the metaverse to move beyond a ‘game like’ interface to virtual systems which accurately reflect real-world ones. Artificial intelligence, digital twins, sensors, and more coalesce to create simulations that mimic real-world actions and inform pro-active decision making.
One of the standout benefits of integrating the metaverse into manufacturing is the capacity for remote operations. By digitally mirroring physical assets in the metaverse, manufacturers can remotely monitor and adjust operations, without the need to be on-site. Put into practice, this could involve overseeing aircraft maintenance from thousands of miles away or adjusting a production line in real-time from a different continent – with full visibility over connected operations. These are the possibilities the industrial metaverse presents.
Fujitsu offers expertise and guidance on how to create a responsible and accurate virtual-physical production environment. Manufacturers can have greater visibility over all parts of their facilities, from who is working in a specific area of a plant to the arrival of new raw materials the next day. Everything across the supply chain that was once hidden from view can be made visible in the metaverse.
Supply chain security and sustainability
Supply chains are increasingly subject to change and disruption. Suppliers, partners, transportation – all links in an ecosystem are being impacted by global and rapid disruptions such as climate change, pandemics, and geopolitical instabilities. As the metaverse synthesizes multiple advanced technologies into a single platform, it is a tool for uncovering paths that seamlessly and successfully navigate through this complexity.
Just as the metaverse can increase productivity within the factory, it brings sustainability benefits to the supply chain as well. Advanced systems can collect data from raw material sourcing to finished goods recycling. This creates an entire supply chain’s worth of data to be considered. By gathering data generated in the digital world and making informed, structural changes to a supply chain’s digital twin, manufacturers can save resources and materials across the supply chain, end-to-end.
But gathering reliable, actionable data in systems beyond immediate control is challenging. Private blockchain is a reliable, recognized innovation for trusted supplier and partner data. The Fujitsu Track and Trust digital ledger solution is built to mirror business processes. It provides a trusted point of validation, transparency, traceability, and verifiability of items throughout their lifecycle. With this data, manufacturers can better control quality and supplier relationships, and they can make more informed planning and forecasting decisions.
Conclusion: The next frontier for Industrial operations
The convergence of AI with the metaverse and other next-gen technologies is creating a new frontier in manufacturing and industrial operations. Companies embracing these transformative technologies will likely find themselves at the forefront of the next industrial revolution, complete with the tools that promote innovation, efficiency, flexibility, and sustainability.
By embracing next-generation technologies, manufacturers can start to implement data-driven decisions and use the iterative power of AI, ML and the metaverse to push the industry forward. Fujitsu's services and solutions guide businesses through this journey, emphasizing growth, reduced waste, and a forward-focused operational vision.
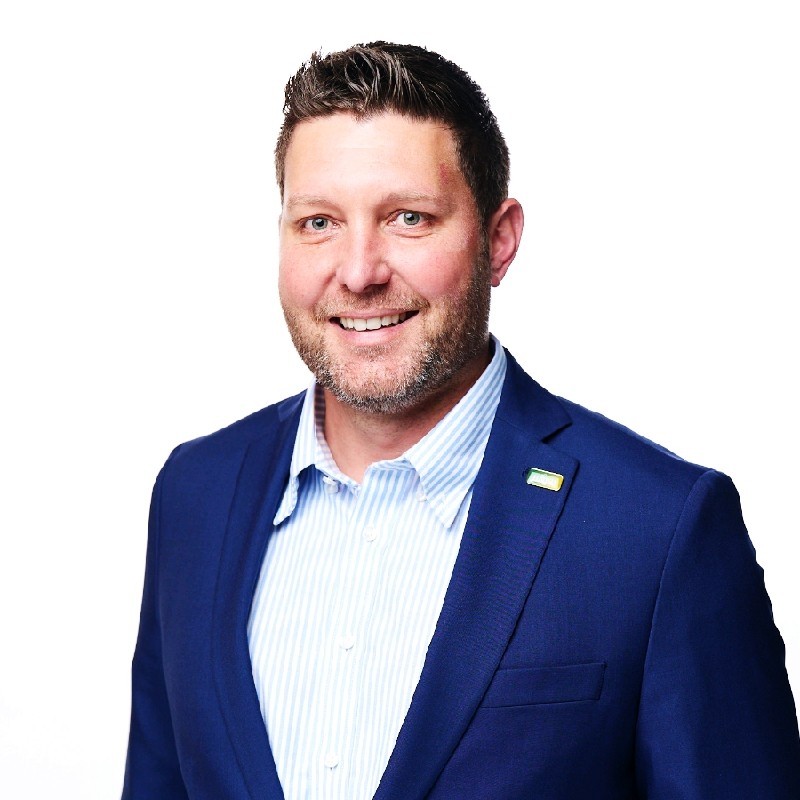
Johan’s overall focus has been on the digital enablement and automation of key manufacturing capabilities and ability to drive compelling value to Fujitsu clients.
Editor's Picks
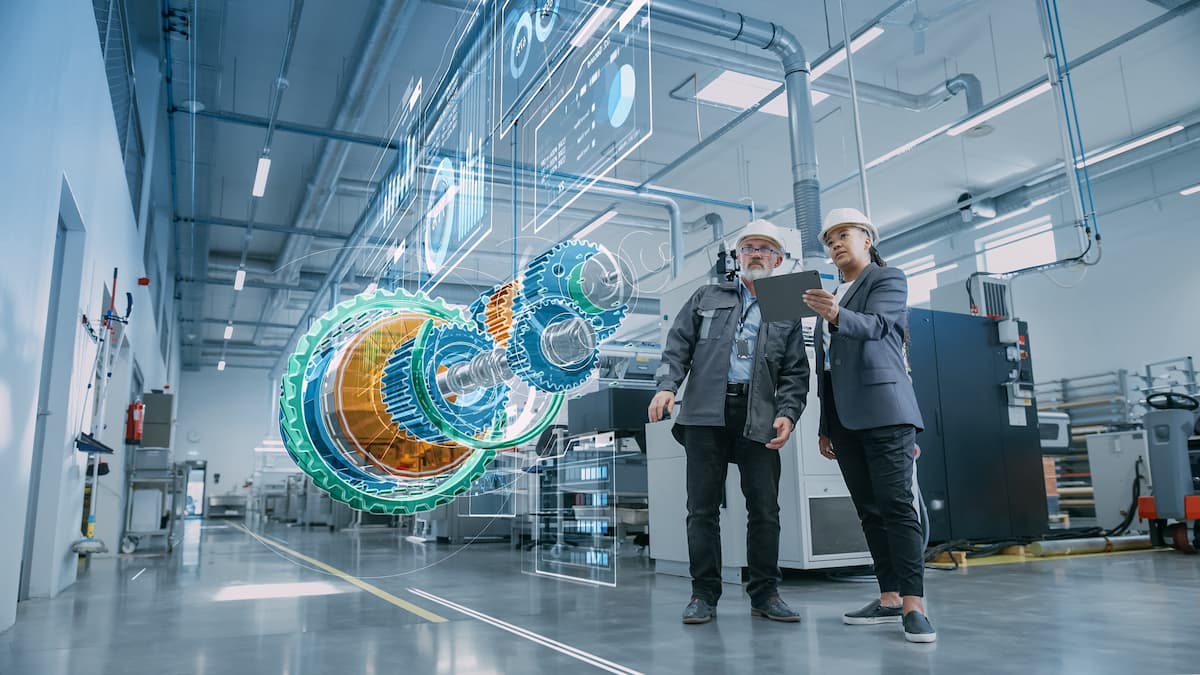
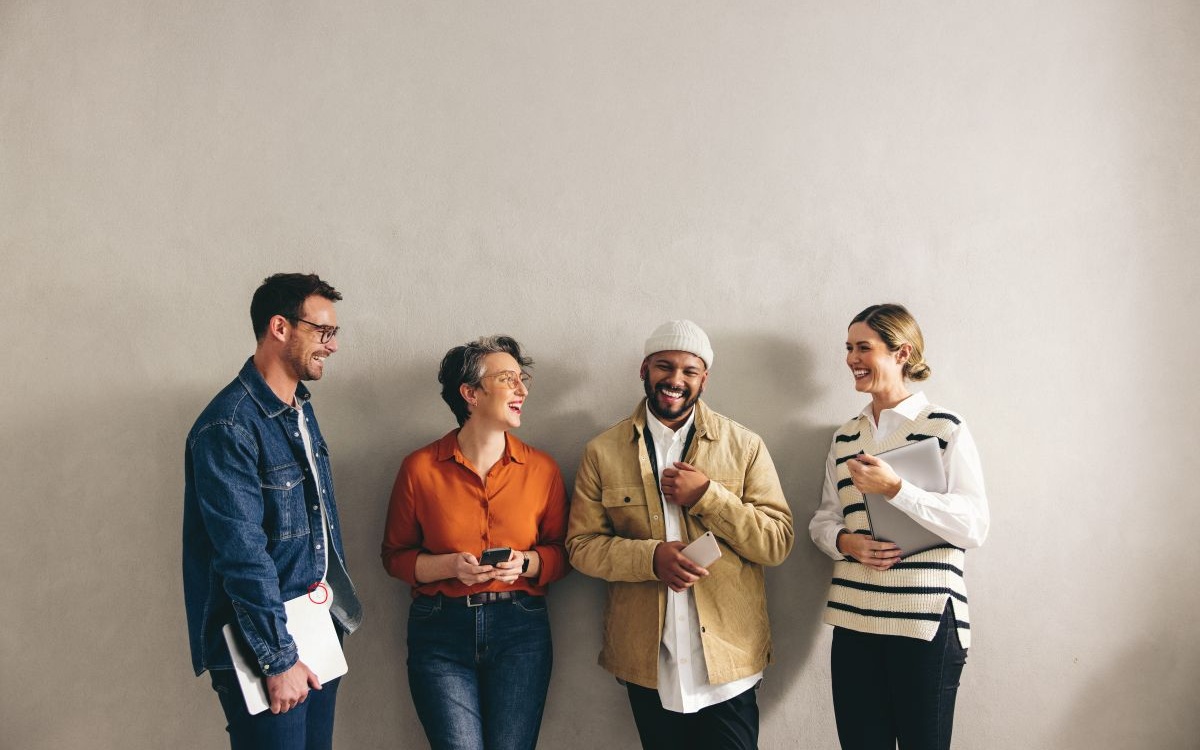
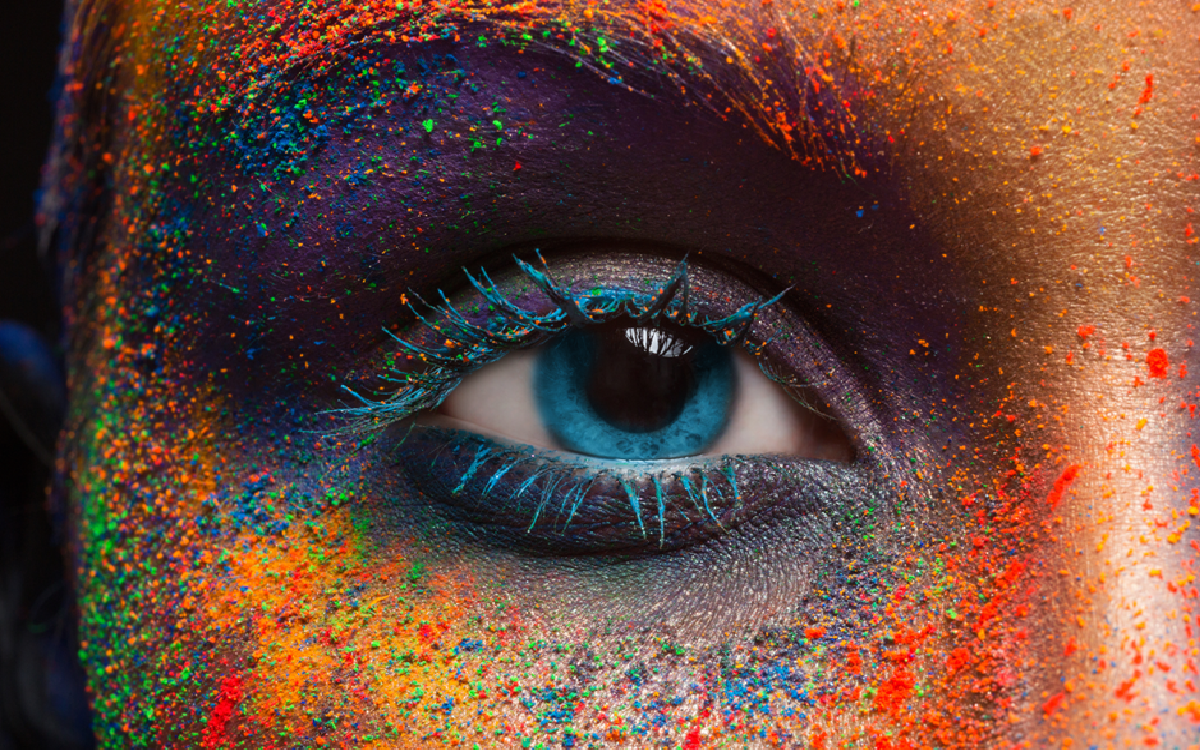