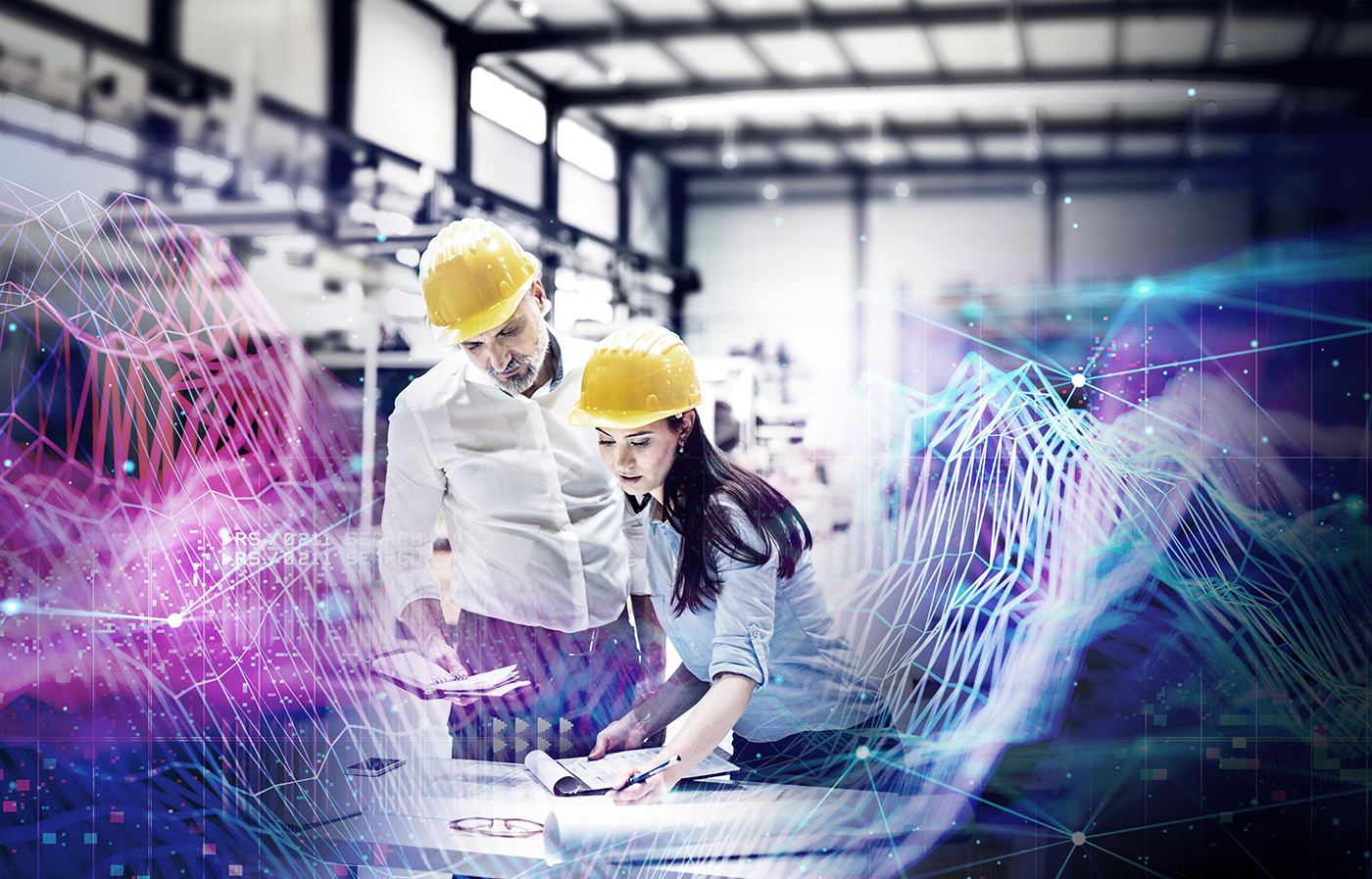
Reijo Sihvonen, Head of Manufacturing – Finland, Fujitsu
Picture a traditional factory. It’s probably a vast building, tucked away in a quiet corner of an industrial estate.
But the key point is that the factory has often been isolated from the rest of the manufacturing enterprise, in not only its location, but its operations and – more recently – its operational technology (OT) and IT network.
Today, trends in manufacturing have challenged that model. In an uncertain economic climate, businesses need greater efficiency and throughput on factory floors.
Consumers are more interested in the provenance and sustainability of what they buy than ever before. And there’s even the chance to sell services on top of products, and drive whole new streams of revenue.
To capitalise on these opportunities, manufacturers are digitalising their operations, to generate actionable real-time data: in other words, creating smart factories that sit right at the heart of the connected enterprise.
Emerging technologies, from blockchain to quantum computing, are also creating new opportunities in this area.
But creating a smart factory is a journey – and it can be very difficult to chart the best route forward.
And given current economic pressures, manufacturers pointed to cost as the biggest hurdle to smart factory initiatives (58%), in our recent research.
Importantly, to date, most smart factory projects haven’t yet delivered a return on investment (56%), which may be making further projects difficult.
This blog will explore three ways that smart factories can deliver meaningful value for manufacturers, by using emerging technologies to capitalise on current trends.
- Connected for the customer
Creating a connected factory provides the opportunity for manufacturers to offer whole new services to customers.
In fact, improving customer experience is by far the most popular external goal for smart factory initiatives (62%) – although the form that takes varies depending on the manufacturer’s target customer.
In the consumer market, there’s a growing trend towards personalization, as customers flock to producers that can deliver items to their specifications.
Both connectivity and efficiency will be key for this move towards Lot Size One, and half of manufacturers are pursuing smart factory projects to enable the more efficient customisation of their products (47%).
Connectivity can also help to bring the unique selling points of products to life for consumers. For example, at Jim Beam, every barrel of whisky is carefully matured for several years; now using the Internet of Things, the company can not only track the production of each individual barrel, but bring that story to life for its consumers.
But in the B2B space, a manufacturer’s competitive edge often comes from servitization; the differentiator might be after sales support, field services or even the -as-a-Service style supply of goods or components after the purchase.
In both cases, connectivity between the factory and the enterprise is key. Customers might need detailed information on availability and logistics to make their purchasing decision, while of course the factory needs to be able to deliver highly customised orders.
But implemented correctly, and the smart factory presents the opportunity to evolve the relationship between the manufacturer and its customers.
- Upping the factory’s efficiency
Virtually every manufacturer in history has sought to improve their operational efficiency.
As a result, it’s not surprising that the most common internal goals for smart factory initiatives are improving product quality (50%), followed by improving asset utilisation (47%).
Particularly in highly technical manufacturing, checks are often carried out by the human workforce, in a process that’s time-consuming, expensive and occasionally error-prone. This is particularly concerning for some products, such as wind turbines, where even the smallest deviations can be catastrophic.
Quality control processes may be automated with imaging tools and machine learning. Images such as X-rays can be assessed by the algorithm to identify anomalies and save time.
This approach has significantly benefitted Siemens Gamesa, where the team implemented an ML-based quality control system for their wind turbines which has cut scanning times by 60%.
Emerging computing technology can also significantly improve productivity on the factory floor.
Traditionally, computers have struggled to take on the kind of combinatorial optimization problems common in manufacturing, such as calculating the most efficient routes for pairs of robots to take when painting a car or welding.
But today, quantum-inspired computing systems are available that can provide answers in real-time, to maximise the throughput of robotic systems. And at one of Fujitsu’s factories, the travel distance for the parts pickup operations was reduced by up to 45%.
This can significantly enhance performance and make the smart factory truly smart.
- Traceable and sustainable
Another priority for manufacturers is demonstrating their credentials as a responsible business.
Consumers today are more concerned than ever with knowing the provenance of products, and may even pay more for those that are sustainably sourced.
Equally, traceability may be important for meeting regulatory requirements and even enabling products like food to command a higher price, due to their origin.
Blockchain is emerging as a powerful tool for tracing the progression of products, from raw materials through to the final product.
As an immutable ledger, using blockchain means that information about a product is securely stored and can’t be changed at any point in the supply chain – so consumers can be confident about what they’re getting.
In the case of food, blockchain could enable customers to trace their meals from farm to fork, and check that items in primary production like meat, soya and almonds have been farmed ethically and sustainably.
In this way, smart factories can help manufacturers showcase the quality of their products – and their socially responsible practices.
Defining the business case
Smart factory initiatives can deliver long term benefits for the business, but it’s true that there’s greater pressure than ever in today’s climate to realise return on investment, quickly.
That’s why it’s critical to carefully and clearly define the business case right from the beginning, identifying the use cases that are actually most important – and valuable – for the business.
At some manufacturing organisations, that might be working out a smart solution that can be used in a large number of factories, to enable the technology to be piloted and then widely scaled.
For others, it might be about making small additional investments to get the best use out of systems that are already in place.
For example, there might be OT and IT systems and datasets across the factory that aren’t linked up, leading to missed opportunities. Better integration at the software level could enable significant gains in efficiency or product quality.
In everything, careful planning is key. Gaining external support from experts that not only understand the potential of emerging technologies, but the wider manufacturing landscape, can be hugely beneficial.
Making smart factories a reality
Creating a smart factory is no mean feat. In challenging economic times, it can be tempting to delay investment to put off the costs of new technologies – and avoid the complication of introducing new solutions.
But developing smart factories can enormously increase a manufacturers’ competitiveness, from more intelligent and efficient production through to meeting the rising expectations of customers around the world.
The time to gain a competitive advantage is now. Creating a connected, intelligent factory will be key for manufacturers to succeed.
Read the full report on The Challenges and Opportunities of the Smart Factory