How to harness end-to-end visibility to increase OEE
Fujitsu / November 8, 2023
Manufacturers today stand eye-to-eye with a confluence of significant societal challenges, ranging from climate change ramifications to demographic-driven workforce imbalances. Within this complex landscape, however, lies a silver lining: the promise of transformative solutions that offer resilience, sustainability and operational excellence.
End-to-end visibility equips manufacturers with an unmatched holistic view of their operations. By achieving greater visibility, businesses can adapt, plan, and optimize with precision. At the heart of this is the elevation of Overall Equipment Effectiveness (OEE), a crucial metric that gauges the heartbeat of your factories’ performance.
However, this is no ordinary feat. As manufacturers grapple with external challenges, the vision of a fully transparent, responsive, and optimized operational environment offers a competitive edge. Whether it's navigating geopolitical risks, addressing workforce disparities, or navigating unforeseen market disruptions, end-to-end visibility emerges as the pathway for not only enhanced OEE, but also for sustainable, future-proof, and ethical manufacturing.
End-to-end visibility and efficiency in a smart factory setting
The power of real-time responses
The ability to respond in real-time is a game-changing improvement for manufacturers. Traditional reactive approaches, relying on dated information and after-the-fact adjustments, are no longer viable in the face of today's dynamic market conditions. Instead, the emphasis is on proactive and preemptive strategies, made possible through end-to-end visibility.
Harnessing this unparalleled visibility means factories can monitor operations seamlessly, pinpointing inefficiencies, predicting potential disruptions, and making adjustments instantaneously. It's a shift from being on the back foot to taking charge, optimizing operations, and thus, significantly enhancing OEE.
For example, one of Fujitsu's process manufacturing customers, a leading manufacturer of consumer packaged goods, experienced a transformative leap in their OEE through increased operational visibility, jumping from a 65% baseline to an impressive 85%. This wasn't magic – it was the culmination of integrating real-time insights, which added a staggering 24 million units of production capacity annually.
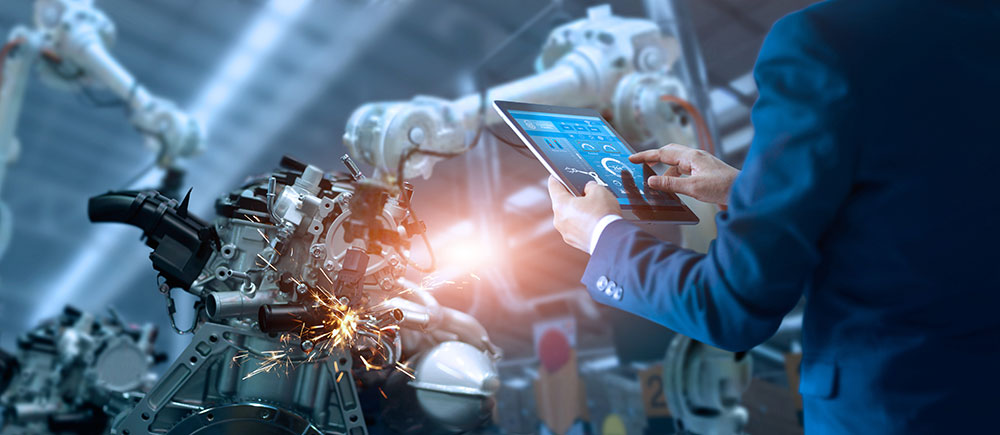
The ability to respond in real-time is a game-changing improvement for manufacturers.
Bridging the gap: legacy factories and modern tech
The manufacturing world is rife with factories steeped in tradition. These so called “legacy” factories are often built on decades-old infrastructure and face unique challenges when seeking to integrate contemporary technologies. They symbolize the storied past of manufacturing but wrestle with the question: How can they remain competitive in the digital age?
The answer lies in retrofitting. While starting from scratch isn't always feasible, strategically standardizing equipment, integrating IoT devices and bringing together disparate data sources in these older facilities can bring new life into them. Capturing and establishing processes around essential data provides a lens of visibility previously unattainable in such environments. By making this leap, these facilities transition towards becoming dynamic entities capable of flexible automation, predictive maintenance, and real-time responses. As a result, legacy factories are empowered to operate with the same efficiency, agility, and insight as their state-of-the-art counterparts.
The rise of flexible automation
In modern manufacturing, agility is paramount. Manufacturers are continually striving to meet the dynamic demands of consumers, often requiring swift changes in production processes. A flexible approach to process automation offers an innovative solution that's revolutionizing the way factories operate.
Traditional manufacturing setups often relied on specialized machines designed for specific tasks. While effective for their purpose, these machines presented limitations when product demands changed, leading to costly downtime and retooling. Industrial process automation, on the other hand, exemplified by robotics, equipped with advanced sensors and programmed for multipurpose tasks, offers a contrasting approach. It provides manufacturers with the versatility to swiftly adapt to changing product specifications, reducing transition times significantly.
Flexible robotics doesn't just offer operational advantages. It also paves the way for cost savings, reduces waste, and ensures consistent product quality. With the incorporation of technologies like AI and machine learning, these robotic systems can also self-optimize, and enhance efficiency even further.
Benefits stretching beyond the factory walls
The financial benefits of visibility
Visibility transcends mere operational oversight – it’s a transformative tool that yields tangible financial outcomes.
By closely monitoring processes, manufacturers can identify bottlenecks, reduce waste, and optimize resources, all leading to significant cost savings. This comprehensive oversight has a direct correlation with OEE, translating to boosted production capacities. An organization's ability to see inefficiencies in real-time can be the difference between profiting and incurring losses, especially in high-volume production scenarios.
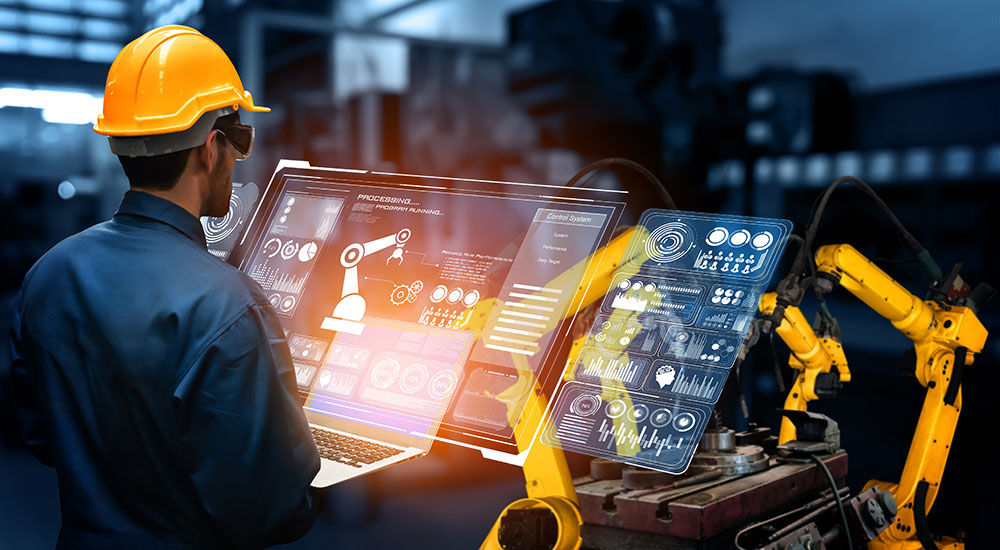
Smart digital factory visibility can yield tangible financial improvement.
Driving sustainability through insight
For manufacturers, sustainability is more than an ethical stance – it's a strategic business imperative that boosts brand loyalty and secures longevity. Gaining full visibility into operations uncovers inefficiencies and wasteful energy usage. Armed with this data, manufacturers can make informed adjustments, such as shutting down energy-consuming idle machinery or adopting energy-efficient methods. This precise oversight reduces waste and production errors, curbing environmental impact and cost.
Moreover, this comprehensive transparency ensures responsible sourcing, guaranteeing materials are ethically procured and sustainably transported. As a result, manufacturers not only protect the environment but also bolster their brand, aligning with the growing demand for eco-conscious products.
Fujitsu’s role in enabling end-to-end visibility
Fujitsu’s expertise: from digital twins to the industrial metaverse
As the manufacturing sector evolves, Fujitsu is playing a crucial role in guiding customers towards a future marked by increased efficiency and unprecedented visibility. Central to our proficiency in this domain are transformative technologies like digital twins and the industrial metaverse.
Digital twins, a concept that involves creating dynamic digital replicas of physical assets, offer manufacturers an unparalleled window into their operations. These digital counterparts enable real-time monitoring, predictive analytics, and scenario simulations, serving as a conduit for proactive decision-making. By mirroring physical assets in the digital realm, manufacturers can anticipate problems, optimize performance, and drive improvements without disrupting ongoing operations.
But Fujitsu's vision extends beyond digital twins. Entering the industrial metaverse, a collective virtual shared space generated by converging physical and virtual realities, Fujitsu is pioneering tools that foster collaborative environments. These environments allow for real-time interaction with digital assets, streamlining design processes, enhancing remote collaboration, and making predictive maintenance a tangible reality. In this metaverse, barriers of geography and time zones dissolve, paving the way for synchronized global operations.
One of the standout benefits of integrating the metaverse in manufacturing is the capacity for remote operations. By digitally mirroring physical assets in the metaverse, manufacturers can remotely monitor, orchestrate, and even tweak operations without the need to be on-site. Imagine overseeing aircraft maintenance scheduling from thousands of miles away or adjusting a production line in real-time from a different continent – these are the possibilities the industrial metaverse presents.
Leveraging Fujitsu's innovations: From quality control to ethical sourcing
To help customers achieve the necessary balance and mutual benefits of growth and sustainability, Fujitsu supports the adoption and integration of the latest in manufacturing innovation.
Quality control (QC) is critical in manufacturing. While traditionally QC relied on manual inspections with the accompanying risk of errors, Fujitsu's AI-driven computer vision solutions have transformed this process. By capturing images and using algorithms to identify defects, this technology reduces manual checks and speeds up inspections. More than just error identification, it facilitates proactive quality management. By understanding defect patterns, manufacturers can preempt issues, thereby mitigating costly recalls and reinforcing brand trust.
Continual optimization also plays an important role. The essence lies in the integration of systems throughout the production cycle, from design to delivery. Fujitsu's approach of closed-loop integration ensures each phase of production informs the next. This continuous feedback loop, enabled by solutions such as Fujitsu Quantum-Inspired Optimization, allows manufacturers to spot inefficiencies, anticipate disruptions, and adapt operations to market shifts. For instance, real-time shop floor data can influence product design, ensuring innovation aligns with existing manufacturing capabilities. Conversely, planning insights optimize shop floor resource utilization.
In today's interconnected world, visibility into supply chains is key. Driven by regulatory norms and informed consumers, there's a pressing need for transparent sourcing practices. Fujitsu's Track and Trust DLT solutions offer a comprehensive view of the supply chain, ensuring ethical material procurement. This clarity not only safeguards against unethical practices but also ensures product quality by tracing raw material origins. In a consumer market gravitating towards ethical brands, responsible sourcing positions manufacturers as frontrunners, catering to the discerning consumers, and allowing them to command premium prices, all while upholding brand integrity.
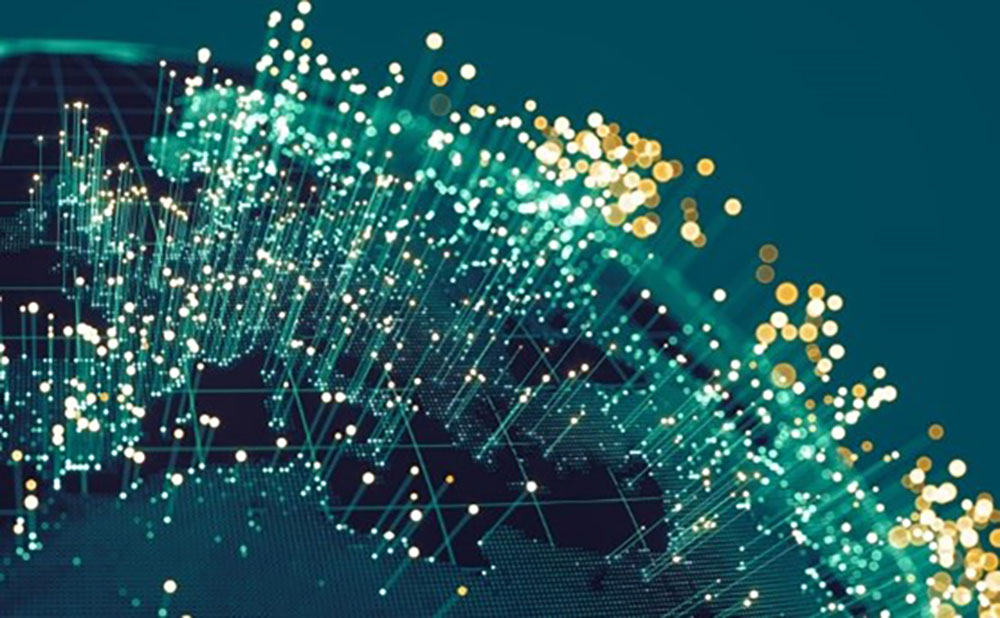
Digital Supply Chain clarity drives product quality and safeguards against unethical practices.
Fujitsu’s collaborations and partnerships
No single entity can encompass the breadth of expertise required to tackle every challenge. Recognizing this, Fujitsu has strategically aligned itself with some of the industry's leaders in digital manufacturing. These partnerships represent a synergy based on technology, domain expertise, and visionary foresight.
Key among Fujitsu's alliances are our collaborations with partners like SAP, Siemens and ServiceNow. With SAP, known globally for its enterprise software solutions, Fujitsu harnesses the power of cutting-edge analytics and business processes. This partnership ensures that manufacturers can access integrated, scalable solutions that enhance their operations from the shop floor to the executive suite.
Siemens, a leader in industrial automation, complements Fujitsu's tech-driven approach. Together, we craft state-of-the-art manufacturing solutions that blend automation, digitalization, and data analytics. These combined strengths ensure manufacturers benefit from best-in-class tools tailored to their specific needs.
As IT and OT systems converge in the manufacturing and utilities sectors, the potential for cyber threats grows exponentially. Recognizing this challenge, Fujitsu and ServiceNow work together to provide a robust solution for OT digital transformation, covering three key OT cyber security services: assessment and asset discovery, network transformation, and 24/7 monitoring. By partnering with cyber security leaders like ServiceNow, Fujitsu delivers OT cyber security as a service, combining global capabilities, industry experience, and standards compliance to ensure maximum uptime and data protection for businesses.
These collaborations empower Fujitsu to offer a more comprehensive suite of solutions, but they also signify a shared vision for the future of manufacturing. By pooling resources and expertise, Fujitsu and our partners are not just responding to the challenges of today but are proactively shaping a more efficient, sustainable, and innovative future for manufacturing.
Seeing the future in clear view
End-to-end visibility has emerged as a fundamental requirement for modern manufacturing. By granting businesses a holistic view of their operations, this visibility highlights existing vulnerabilities and inefficiencies, while also spotlighting areas for growth and enhancement. This approach guides manufacturers through the complexities of today's industrial landscape, ensuring they remain agile, resilient, and ahead of the curve.
Fujitsu, with a rich legacy in technological innovation, plays a critical role in this paradigm shift. By offering tools and strategies ranging from digital twins to blockchain and AI, Fujitsu not only empowers manufacturers with the insights they need but also provides the actionable solutions to act upon them.
In embracing these advancements, manufacturers aren't just optimizing their operations; they're making a commitment to sustainability, to their workforce, to quality, and to the future. As the sector navigates challenges ranging from shifting market dynamics to escalating environmental concerns, such commitments become the anchors that ensure a brighter and more efficient future for manufacturers and society at large.
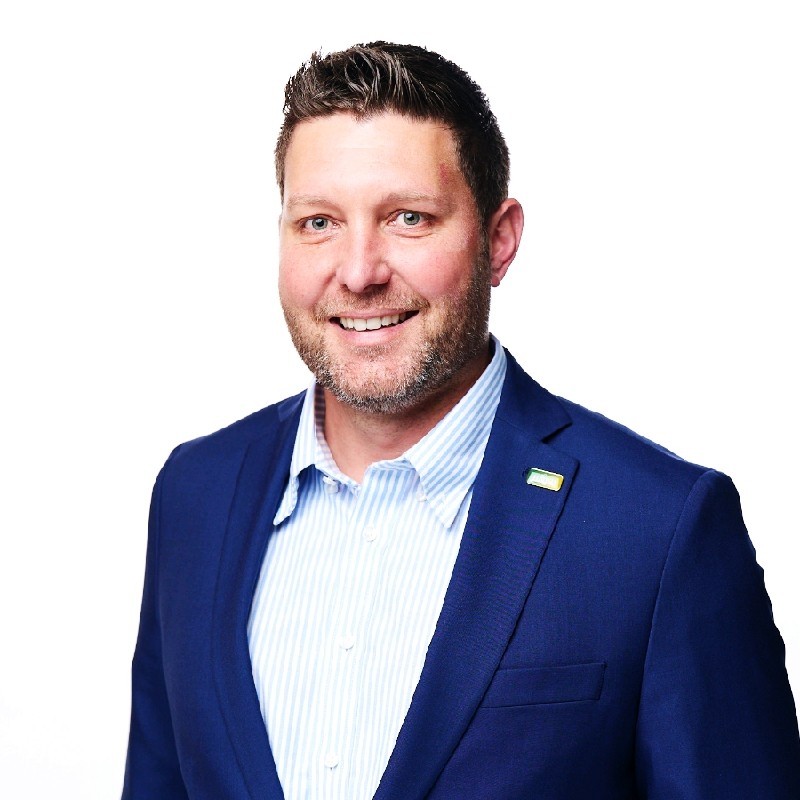
Johan’s overall focus has been on the digital enablement and automation of key manufacturing capabilities and ability to drive compelling value to Fujitsu clients.
Editor's Picks
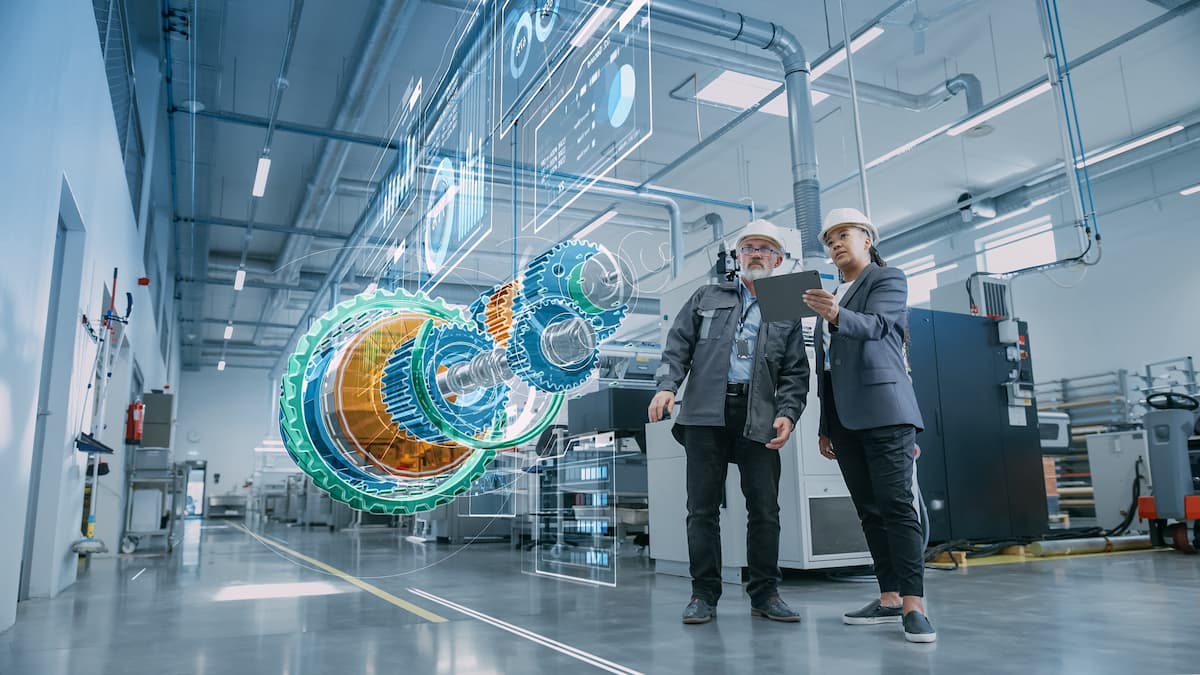
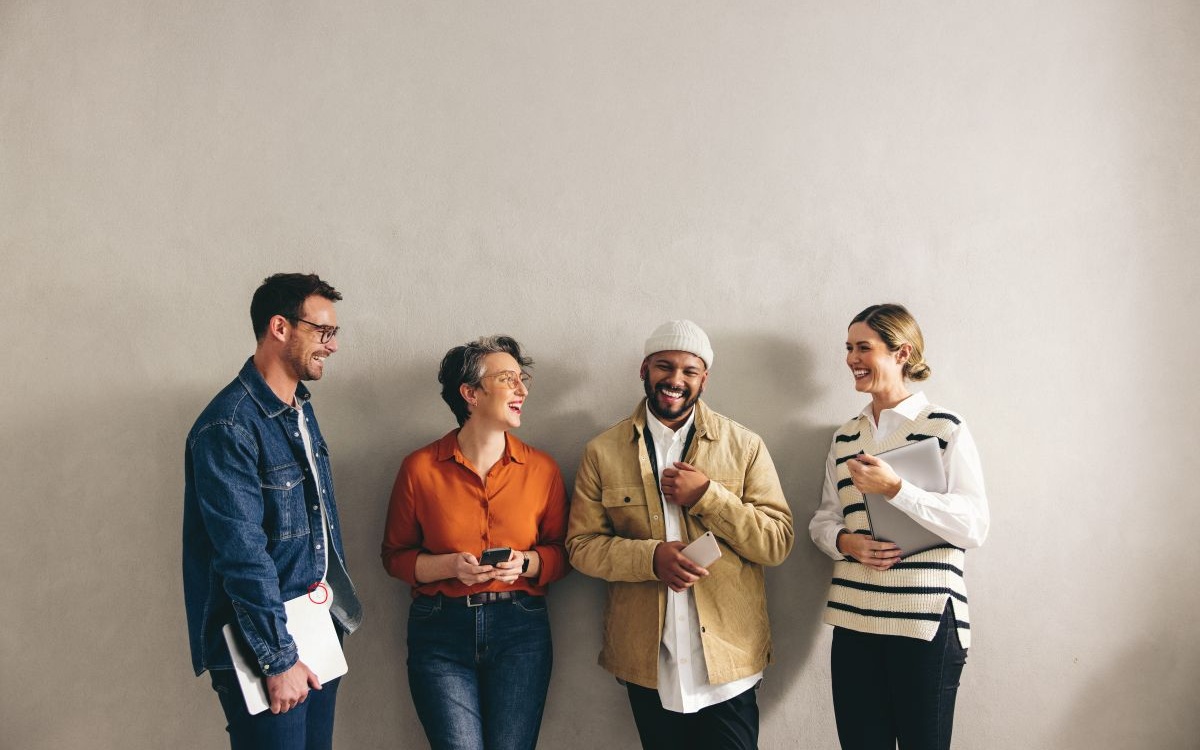
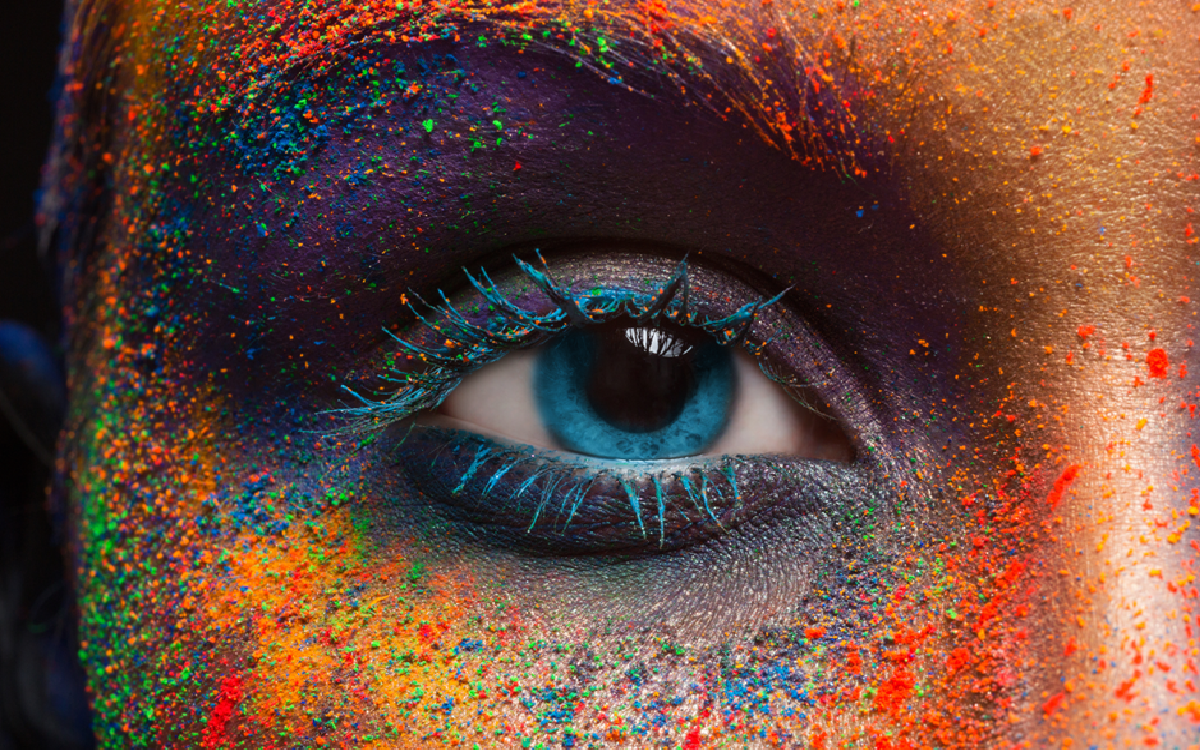