Optimization – The key to next generation resilience in your supply chain
Fujitsu / March 24, 2022
With supply chain disruption set to continue into 2022 and beyond, business leaders must address new ways to optimize the weak links in their chains. Optimization using data and advanced technologies available today, can help make supply chains more resilient. Improved efficiency also results in a happy side effect of improving sustainability targets and helping society address climate change.
An Era of Constant Disruption
After several decades when globalization seemed to offer only upside, the last few years have demonstrated how ever-greater global interdependencies can lead to lasting disruption. The pandemic, shipping disruptions in the Suez Canal, issues relating to Brexit, have all served to undermine the efficiency of the global trading system while also revealing systemic deficiencies in national and global supply chains.
A White House report into recent shortages blamed the issue partly on poor demand forecasting. Manufacturers and suppliers, the report noted, have been unable to track what goes on in intermediate layers. This led manufacturers to cancel orders for components, assuming demand would remain low.
Industry analyst firm PAC turns the spotlight on this in a new white paper , Optimization: The key to next-generation resilience in your supply chain, commissioned by Fujitsu. This paper examines how recent technology advances enable organizations to achieve end-to-end performance improvements and unprecedented resilience – achieved by optimizing systems and strengthening weak links throughout the supply chain.
An Urgent Need for Optimization
Many supply chain processes have become highly complex and are still not optimized despite investment in computing systems. The great thing about optimization is that it can be done from the ground up, looking at individual pieces within the supply chain. Factors such as cost, risk, speed and efficiency must be weighed up to assess end-to-end supply chain efficiency, down to details such as how often to run picking cycles in a warehouse, to which form of transport to use for last-mile delivery.
The extended disruption of the last two years has forced organizations to consider taking a more agile approach to optimization, enabling individual processes within the chain to adapt to rapid changes in market conditions and accelerate the return on investment. Long-term transformation programs are no longer an option, and shorter-term solutions are urgently needed.
Optimization is hardly a new idea for manufacturers. It has been an essential ingredient in every industrial revolution, from using powered machines to enhance and optimize physical tasks previously done by people through to innovations like Kaizen (continuous improvement), the Toyota Production System and Kanban to improve further the way things are built. The industry 4.0 revolution takes the baton and builds on its optimization legacy.
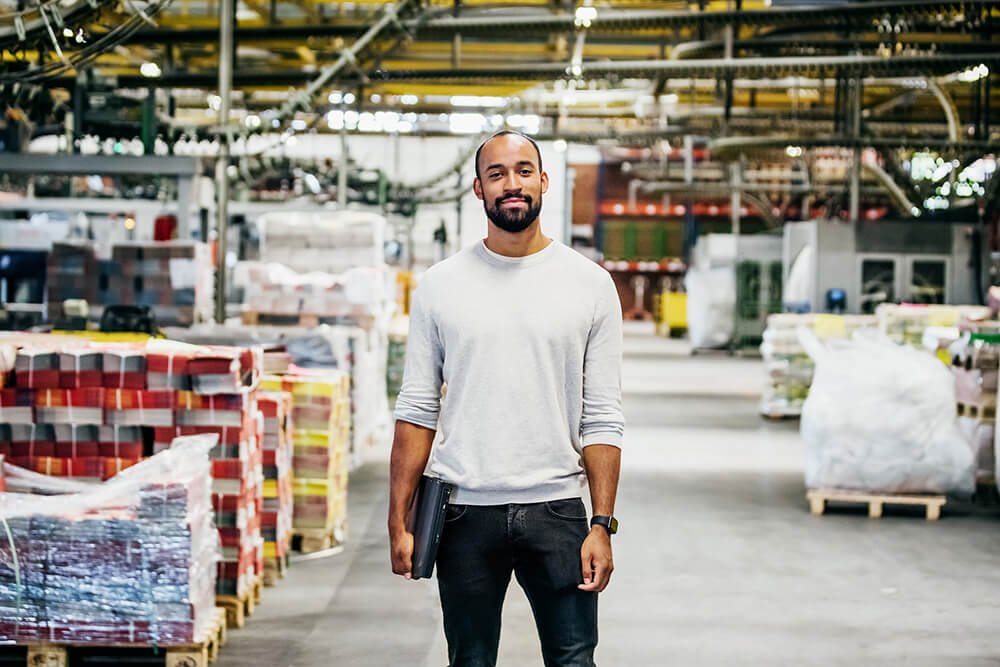
Optimization in Action
The main bottleneck holding back further optimization today is that command and control becomes a less efficient management tool with every increase in complexity. Single points of failure damage the entire system until responses are received from the top.
Technology has struggled to overcome the optimization challenge because real life gets complicated very quickly. When you increase the number of variables — such as the number of stops on a route, the number of parcels a driver is dropping off, or the number of jobs in a machine shop —then the amount of compute time needed to find the best solution can increase very rapidly. This is particularly true if you need to consider a set of parameters like the priority of a task or the weight of a package at each point.
Traditional supply chain systems have lacked the power to quickly process these combinations. Today, a growing number of organizations across multiple industry sectors are now tackling the complexity challenge head-on using the latest quantum-inspired optimization technology.
To make this point clear, the white paper looks at examples in warehousing, production scheduling and trucking. In warehousing, for instance, quantum-inspired optimization now makes it possible to optimize picking efficiency by size, weight, or the order in which items arrived, and other factors. This has already led to a 20% reduction in pickers’ travel today and the potential for further reduction to 45% by calculating the optimum position of each SKU in the warehouse.
This and the other examples in the paper are real breakthroughs. We’ve seen machine learning blossom over the last five years as computers capable of running the models became increasingly accessible. Quantum-inspired optimization is at that exact point – with firms wanting to steal a march on their competition looking at how they can leverage it.
To help you start the journey to a simpler, more optimized supply chain, Fujitsu is making the white paper available as a free download. Here you can read PAC and Fujitsu’s recommendations for the next steps to harness the power of optimization — something that should be on the radar of every supply chain leader as they rebuild in 2022.
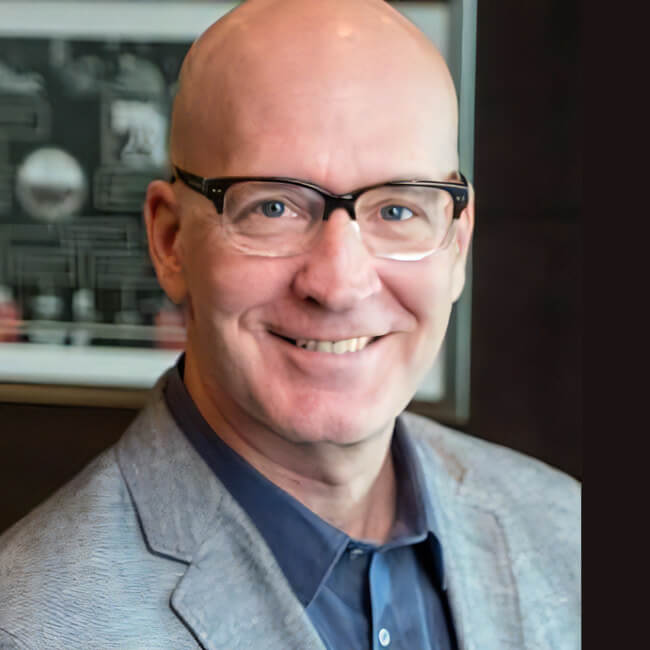
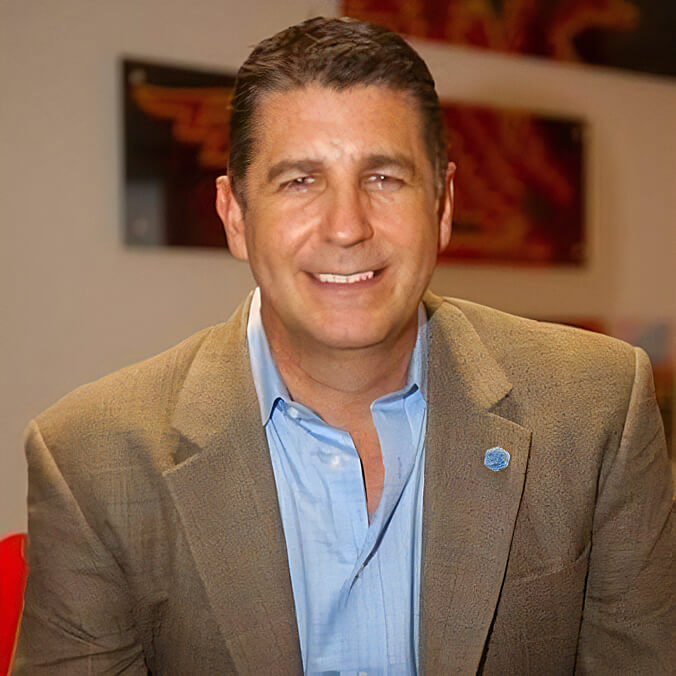
Related information
Editor's Picks
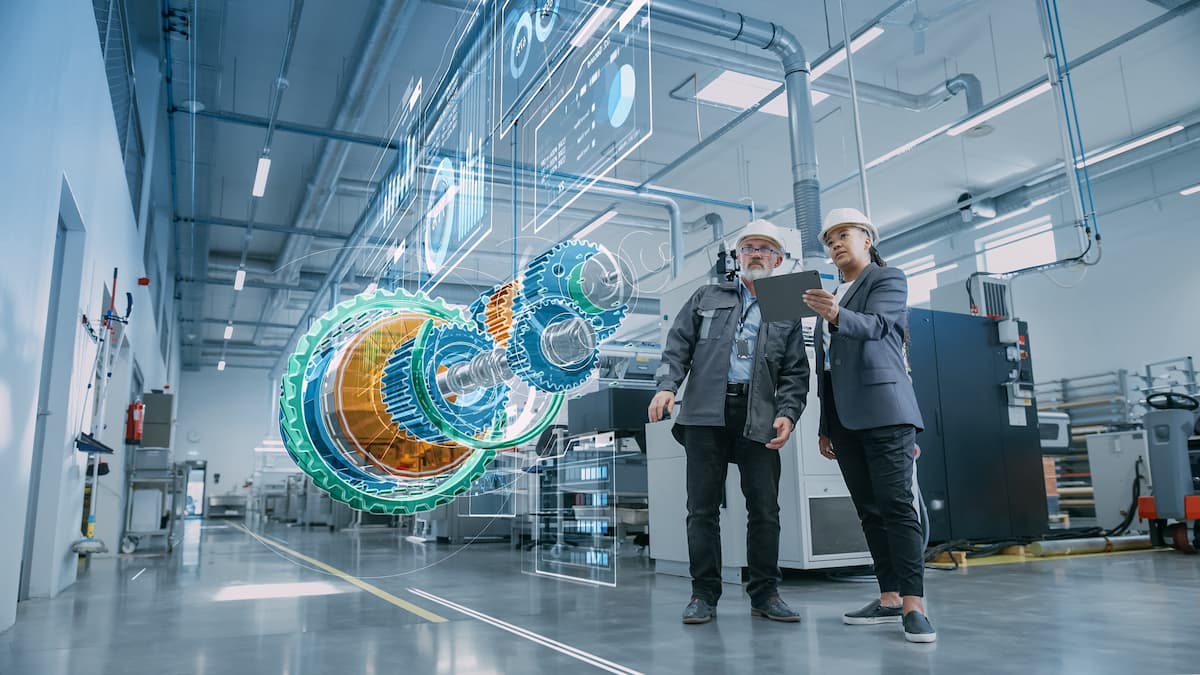
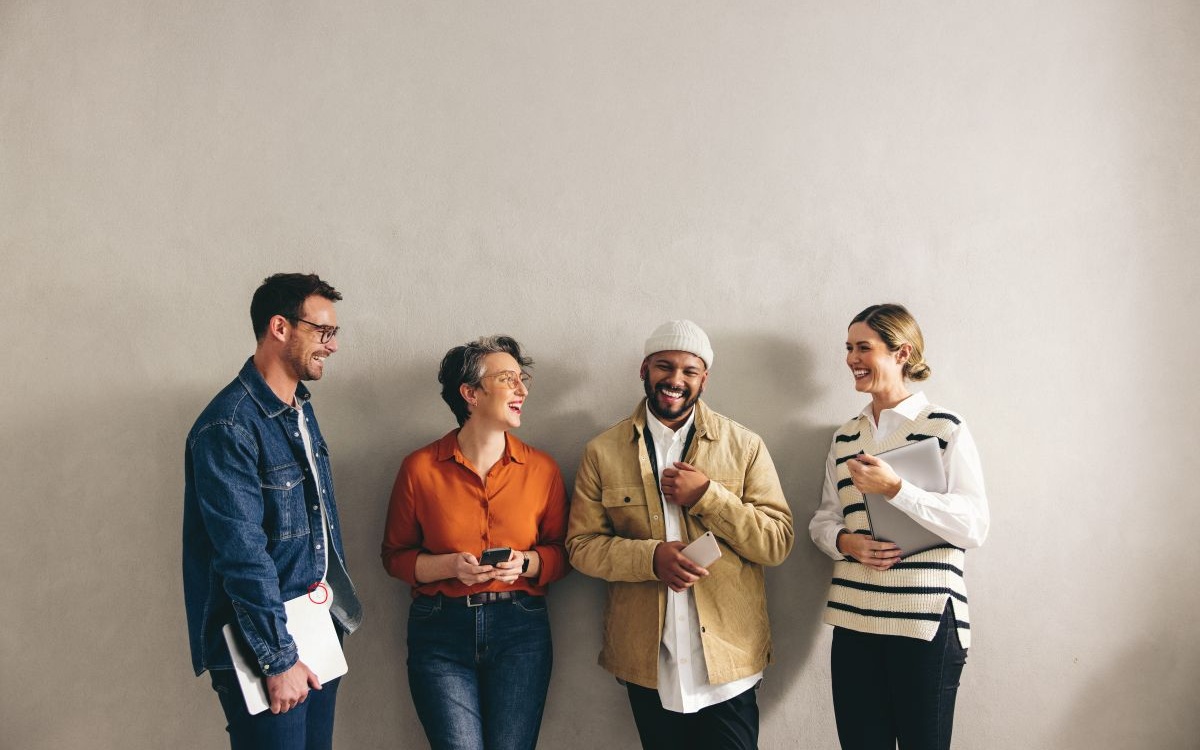
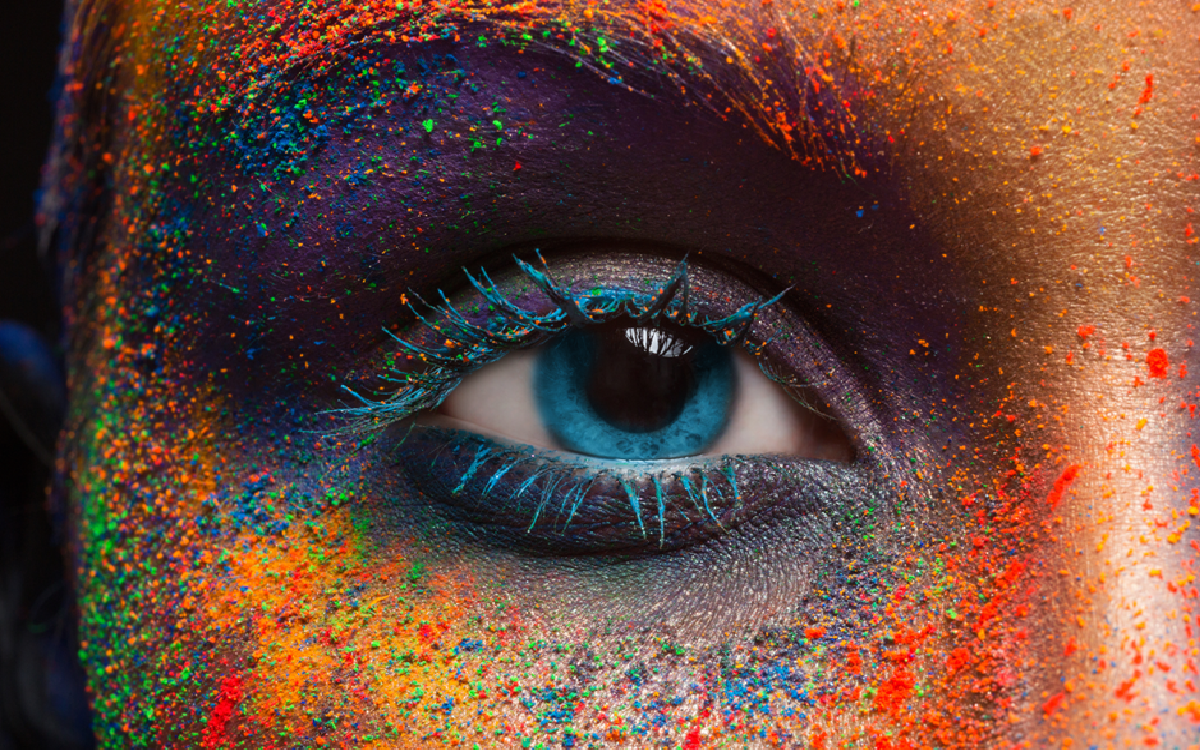